جدول المحتويات
What Exactly is an Interior Model? تفريغ المفهوم
في قلبها, an interior model is a physical scale model focused specifically on the inside of a building or structure. It showcases the arrangement of rooms, أثاث, المباريات, التشطيبات, and overall spatial quality. But the term covers a spectrum of creations.
Defining the Scope: From Simple Concepts to High-Detail Replicas
Not all interior models are created equal. Their complexity directly relates to their intended purpose:
- النماذج المفاهيمية / نماذج رسم: Often made quickly and with simple materials (like cardboard or foam), these early-stage models explore basic layouts, volumes, والعلاقات المكانية. They’re great for testing initial ideas and broad concepts. Think of them as 3D brainstorming tools.
- نماذج العمل: These are more defined, incorporating more precise information about materials, ترتيبات الأثاث, and lighting concepts. They are used during the design development phase to refine ideas and make key decisions.
- عرض تقديمي / Execution Models: These are highly detailed, finely finished models intended for client presentations, marketing purposes, or final design approval. They showcase materials, الألوان, إضاءة, and furniture with a high degree of realism and aesthetic appeal. These are the models that often wow potential buyers or investors.
- Scale Mock-ups: أحيانا, full-scale (1:1) or large-scale sections of an interior are built to test specific functionalities, ergonomics, material applications, or user experiences directly.
The Core Purpose: Making the Intangible Tangible
Why go to the trouble of building a physical model? Because it achieves things that other methods struggle with:
- Bridging the 2D-3D Gap: Models transform flat floor plans and elevations into a readily understandable three-dimensional space. You can grasp height, عمق, volume, and perspective in a way that requires significant interpretation from drawings.
- Visualizing Spatial Relationships: How does the living room flow into the kitchen? Is there enough space around the conference table? How does the light from that window hit the back wall? Models make these relationships immediately apparent.
- Representing Atmosphere and Ambiance: Through careful selection of materials, الألوان, وتأثيرات الإضاءة, models can convey the intended mood and feel of a space much more effectively than abstract descriptions.
- Facilitating Tactile Exploration: The ability to physically look into, touch (carefully!), and interact with the model provides a deeper level of understanding and connection than viewing a screen.
“A three-dimensional model represents how different elements can be understood or work with each other… [هو - هي] translates into a common language that doesn’t give rise to misunderstandings.”
Distinction from Other Model Types
While sharing techniques with architectural exterior models or industrial models, interior models are uniquely focused on the lived experience within a space. The emphasis is less on the external form or industrial process, and more on layout, المفروشات, التشطيبات, إضاءة, human scale, and the overall interior environment.
The Crucial Role and Importance of Interior Models
Interior models are far more than just decorative objects; they are fundamental tools that drive success throughout the architectural and design process. Their importance stems from their ability to enhance visualization, تواصل, decision-making, وفي النهاية, the quality of the final built space.
Why Use Interior Models? Core Benefits at a Glance
Investing time and resources into creating an interior model yields substantial returns. Here’s a snapshot of the key advantages:
Benefit Category | Key Advantage |
---|---|
تصميم & تخطيط | Improved Visualization & Spatial Clarity |
Effective Design Evaluation & Refinement | |
Early Error Detection & Cost Savings | |
تواصل & Engagement | Enhanced Communication & Understanding |
Increased Client Involvement & Satisfaction | |
Aids Regulatory Approvals | |
تسويق & عرض تقديمي | Powerful Marketing & Sales Tool |
Impact on the Design Process
Interior models are integral to the iterative nature of design:
- Concept Development Aid: They help solidify initial ideas and explore different spatial configurations quickly.
- Detailed Design Validation: As designs become more specific, models allow designers to check clearances, خطوط الرؤية, furniture fit, and the interplay of materials and light.
- Facilitating Informed Decisions: By presenting options tangibly, models empower both designers and clients to make better choices regarding layout, مواد, التشطيبات, and furniture.
- Reducing Risk: Identifying potential design flaws or construction issues at the model stage significantly reduces the risk of costly changes later in the project.
Necessity for Clarity and Complex Projects
For intricate interior layouts, multi-level spaces, or projects involving numerous stakeholders, the clarity provided by a physical model is often indispensable. It cuts through the ambiguity of drawings and ensures everyone involved shares a common, accurate understanding of the proposed design.
The Step-by-Step Process of Bringing an Interior Model to Life
Creating a compelling interior model is a journey that requires careful planning, precise execution, and often, a blend of traditional techniques and modern technology. Let’s walk through the typical phases involved.
مرحلة 1: Conceptualization and Design Foundation
Like any design project, it starts with understanding the goals.
- Define Purpose and Scope: What should the model communicate? Who is it for? What level of detail is required (conceptual, working, عرض تقديمي)? What is the budget and timeline?.
- Gather Information: Collect architectural plans, الارتفاعات, أقسام, furniture layouts, عينات المواد, لوحات الألوان, and any relevant sketches or renderings.
- Initial Sketches and Planning: Develop preliminary ideas for the model’s construction, حجم, and key features.
The Critical Role of Drawings and Plans
Accurate source material is essential. Architectural drawings (floor plans, أقسام, الارتفاعات) provide the geometric foundation. Interior design plans specify furniture placement, التشطيبات, and fixtures.
مرحلة 2: Digital Design (Optional but Recommended)
While not always mandatory for simpler models, using CAD often enhances precision and facilitates fabrication.
- Creating Digital 3D Models: Using software like SketchUp, أوتوكاد, ريفيت, or Rhino, designers create a precise digital version of the interior space and its components.
- Virtual Visualization: Allows for checking proportions, clearances, and generating views before physical construction.
- Generating Fabrication Data: CAD files can directly drive laser cutters and 3D printers, ensuring accuracy in part production.
مرحلة 3: Material Selection – Choosing the Right Medium
The materials used significantly impact the model’s look, feel, متانة, والتكلفة. Choices depend on the desired level of realism and the scale.
مادة | صفات & Uses in Interior Models |
---|---|
Foam Board / Foamcore | خفيف الوزن, من السهل قطع, good for walls, الأرضيات, basic structures, massing models. White surface takes paint well. |
كرتون / Cardstock / Paper | Versatile for walls, simple furniture shapes, representing wall coverings, flooring patterns, easy to fold/cut. |
خشب (البلسا, Basswood, الخشب الرقائقي) | Easy to carve/shape (البلسا), good for furniture, تقليم, العناصر الهيكلية, baseboards. Provides natural texture. |
Plastics (الستايرين, Acrylic/Plexiglass) | Styrene is flexible, good for fine details, تقليم. Acrylic is rigid, clear, great for windows, glass partitions, display cases. Both paint well. |
3D Printed Plastics/Resins | Excellent for complex shapes, custom furniture, تفاصيل معقدة, المباريات. Huge variety of materials possible. |
Fabric / Textile Samples | Essential for realistically representing upholstery, curtains, rugs, bedding. Adds texture and color. |
فخار / Modeling Putty | Good for sculpting small, unique decorative objects, organic shapes, or custom fixtures. |
Paint / Finishes / Graphics | Crucial for color accuracy, simulating textures (الحبوب الخشبية, tile), adding details via printed graphics applied to surfaces. |
Strategic use is key; sometimes representing every single texture can look cluttered. Focusing on key materials or using monochrome can emphasize form and layout.
مرحلة 4: Fabrication and Construction – Building the Model
This is where the model takes physical shape.
- Cutting Components: Precisely cutting walls, الأرضيات, furniture parts using knives, مناشير, قواطع الليزر, or CNC machines based on plans or CAD data.
- 3د الطباعة: Producing complex or custom components like furniture, المباريات, or decorative elements layer by layer.
- Shaping and Forming: Bending plastics, carving wood or foam, sculpting clay elements.
- Assembling the Structure: Carefully joining walls, الأرضيات, and ceilings to create the basic spatial enclosure. Accuracy is critical here.
Essential Tools for the Task
Precision requires the right tools:
- أدوات القطع: Utility knives, scalpels, razor saws, potentially a small bandsaw or scroll saw, laser cutter.
- أدوات القياس: Steel rulers, scale rulers, calipers, squares, measuring tapes.
- مواد لاصقة: White glue (PVA) for wood/paper, plastic cement for styrene, super glue (cyanoacrylate) for quick bonds, epoxy for strength.
- Shaping/Finishing Tools: ملفات, sanding blocks/paper, tweezers, clamps, small drills.
مرحلة 5: Assembly and Finishing – Adding Realism and Detail
This stage brings the model to life.
- Installing Interior Elements: Placing windows, الأبواب, built-in cabinets, and fixtures.
- Furnishing the Space: Carefully arranging miniature furniture according to the design plan. Furniture might be custom-built, 3D printed, or purchased pre-made scale items.
- Applying Finishes: Painting walls, applying textures, adding flooring materials (printed paper, thin veneer, textured paint), representing tile or wood patterns.
- Adding Decor: Placing small details like rugs, curtains, مصابيح, artwork (miniature paintings!), النباتات, and accessories to create a lived-in feel. “Even the smallest detail holds the promise of grandeur”
مرحلة 6: Integration of Lighting (Optional but Impactful)
Adding lighting dramatically enhances realism and ambiance.
- تخطيط: Determining placement of light sources (ceiling fixtures, مصابيح, under-cabinet lights, natural light simulation through windows).
- Technology: Miniature LEDs are commonly used due to their small size, low heat, and energy efficiency. Fiber optics can create subtle effects.
- Wiring: Careful, concealed wiring is necessary, often running through walls or under the baseboard, connected to a power source (battery or transformer).
- Control: Lighting might be simply switched on/off, or more complex systems could allow dimming or control of individual circuits.
- Effect: Lighting helps define mood, highlight focal points, and demonstrate how both natural and artificial light will function in the space.
مرحلة 7: Testing, تقييم, and Refinement
Before completion, the model is reviewed.
- Accuracy Check: Comparing the model against the plans for dimensional accuracy and correct placement of elements.
- Visual Review: Assessing the overall aesthetic, color fidelity, finish quality, والواقعية.
- Functional Check (if applicable): Testing any moving parts or lighting systems.
- Refinement: Making necessary adjustments based on the review – touching up paint, adjusting furniture placement, fixing any construction flaws.
مرحلة 8: Final Presentation and Protection
- تنظيف: Ensuring the model is free of dust and fingerprints.
- Base and Casing: Often mounted on a sturdy, presentable base. A clear acrylic cover (بيربيكس) is frequently used to protect the model from dust and damage, especially for display models.
- Photography/Documentation: Professionally photographing the model (see next section) is crucial for portfolio and communication purposes.
- Delivery/Presentation: Safely transporting and presenting the model to the client or intended audience.
Key Characteristics Defining High-Quality Interior Models
A successful interior model possesses several key attributes:
- Accurate Scale and Proportion: Faithfully represents the size relationships between the room, أثاث, and occupants.
- Clear Spatial Representation: Effectively communicates the layout, volume, circulation, and feel of the interior space.
- Convincing Detail Level: Includes appropriate details in furniture, المباريات, التشطيبات, and decor to convey the design intent realistically.
- Realistic Materiality and Texture: Uses materials and finishes skillfully to simulate the appearance and feel of real-world surfaces.
- Thoughtful Lighting Integration (if included): Lighting enhances realism, defines mood, and accurately portrays illumination effects.
- High Level of Craftsmanship: Exhibits clean construction, precise assembly, flawless finishing, and overall attention to detail.
- Durability and Presentation: Well-constructed on a stable base, often with a protective cover, suitable for display and handling.
The Multifaceted Benefits of Utilizing Interior Models (Detailed Exploration)
Let’s expand on the advantages of incorporating interior models into the design and communication workflow.
Benefits in Design, تخطيط, and Problem Solving
- Unparalleled Visualization: Models offer an intuitive grasp of three-dimensional space that flat drawings struggle to convey. You can immediately see ceiling heights, room volumes, and how light plays within the space.
- Early Identification of Design Flaws: Awkward furniture placement, insufficient clearance, poor sightlines, or conflicting design elements become readily apparent in a physical model, allowing for correction before costly construction. Imagine realizing a door swing conflicts with furniture *before* the walls are up!
- Testing Layouts and Flow: Physically arranging miniature furniture or tracing circulation paths within the model provides invaluable insights into the functionality and efficiency of a layout.
- Understanding Scale and Proportion: Models make abstract dimensions concrete. Clients and designers can better judge if furniture pieces are appropriately scaled for the room or if architectural elements feel proportionally correct.
- Material and Finish Evaluation: While not perfect replicas, models allow for testing combinations of colors, القوام, and materials in context, helping to visualize the overall aesthetic.
- Promoting Creative Problem-Solving: Interacting with a physical representation can spark new ideas and innovative solutions to design challenges that might not emerge from screen-based work.
Benefits in Communication and Collaboration
- Universal Language: Models transcend technical jargon. They provide a clear, shared understanding for clients, المقاولون, المصممين, وأصحاب المصلحة الآخرين, regardless of their ability to read complex drawings.
- Focused Discussions: Meetings centered around a model tend to be more productive. Participants can point directly to elements, discuss specific spatial relationships, and provide targeted feedback.
- Reduced Misunderstandings: The clarity offered by a model significantly reduces the potential for misinterpretations of the design intent, leading to fewer conflicts down the line.
- Facilitating Approvals: Presenting a clear, professional model can help expedite design approvals from clients or regulatory bodies by making the proposal easier to understand and evaluate.
Benefits in Client Engagement and Satisfaction
- Tangible Connection: Clients can see, touch (carefully!), and visually ‘walk through’ their future space, creating a much stronger emotional connection and sense of ownership than viewing drawings.
- Empowered Decision-Making: When clients truly understand the design, they feel more confident making decisions about finishes, أثاث, and other details.
- Managing Expectations: A realistic model helps set accurate expectations about the final outcome, reducing the potential for disappointment later.
- Increased Investment: Clients who feel involved and understand the vision are often more invested (both emotionally and financially) in the project’s success.
Benefits in Marketing, Sales, and Presentation
- Compelling Sales Tool: In real estate development, models are proven tools for attracting buyers and conveying the quality and lifestyle of a property.
- Enhanced Presentations: Models elevate any presentation, making it more dynamic, memorable, and professional. They demonstrate a high level of commitment and design thinking.
- Showcasing Expertise: A well-executed model serves as a tangible example of the designer’s or architect’s skill, الاهتمام بالتفاصيل, and ability to create desirable spaces.
- Attracting Attention: Whether in a sales center or at an industry event, a detailed interior model naturally draws interest and sparks conversation.
Types of Interior Models
Interior models can be categorized in various ways, helping to understand their specific roles and characteristics.
Classification by Purpose/Stage
Based on Article 9 and common practice:
- النماذج المفاهيمية: Built early to simulate spatial qualities simply, often using basic materials to explore ideas and massing quickly.
- نماذج العمل: Used during design development to define and refine ideas. They contain more precise (but often still modifiable) information about materials, أثاث, والإضاءة.
- Execution/Presentation Models: مفصلة للغاية, finished models built to present the final design proposal for discussion, موافقة, or marketing. These often showcase specific furniture choices and finishes.
Classification by Scope
Based on Article 11 and general types:
- Room Models: Focus on a single interior space like a living room, kitchen, or office.
- Floor Plan Models: Show the layout of an entire floor or apartment unit, illustrating the arrangement and connection of multiple rooms.
- Section Models: Cut through a building or room vertically to reveal the internal structure, طبقات (wall/floor construction), or relationships between levels.
- Furniture Models: Models specifically focused on representing individual pieces or sets of furniture, often at a larger scale for detail.
Classification by Application Area
Based on Article 5:
- Residential Interior Models: Homes, الشقق, condos.
- Commercial Interior Models: Offices, retail stores, المطاعم.
- Hospitality Interior Models: Hotels, منتجعات, clubhouses.
- Healthcare Interior Models: Hospitals, clinics, labs (Focus on functionality and compliance).
- Educational Interior Models: Schools, universities, libraries (Highlighting learning environments).
- Exhibition and Museum Interior Models: Display layouts, visitor flow.
- Public Building Interior Models: Libraries, community centers, government offices.
المادية مقابل. النماذج الرقمية
While this guide focuses on physical models, it’s important to acknowledge digital alternatives:
- النماذج الرقمية: Created using CAD or 3D modeling software. Offer flexibility for quick changes, easy sharing, and advanced rendering/simulation.
- النماذج المادية: Offer tactile interaction, intuitive spatial understanding, and a strong presentation presence.
- Synergy: غالباً, both are used. Digital models aid the design and fabrication of physical models. Physical models provide tangible validation and communication.
Technology’s Role in Modern Interior Model Making
Technology has profoundly impacted how interior models are designed and built, enabling greater precision, تعقيد, and efficiency.
تصميم بمساعدة الكمبيوتر (كندي) & بيم
- Foundation for Precision: Software like AutoCAD, ريفيت, سكيتش اب, Rhino provides the digital blueprint, ensuring dimensional accuracy.
- BIM Integration (ريفيت): Allows models to be data-rich, incorporating information about materials and components beyond just geometry.
- Visualization Power: Enables realistic renderings and virtual walkthroughs before physical construction starts.
Additive Manufacturing (3د الطباعة)
- Detail and Complexity: Ideal for creating intricate furniture, custom fixtures, decorative elements, or complex architectural details that would be difficult or time-consuming to make by hand.
- Speed and Iteration: Enables rapid prototyping of design elements, allowing for quick testing and refinement.
- Material Options: From standard plastics to high-resolution resins and even full-color printing, offering diverse aesthetic possibilities.
تصنيع CNC & قطع الليزر
- قطع الدقة: CNC routers can accurately mill wood or plastic for structural parts or furniture components. Laser cutters excel at precisely cutting flat materials like acrylic, thin wood, or cardstock for walls, flooring patterns, or decorative screens.
- Consistency: Ensures uniformity when multiple identical parts are needed.
التصور المتقدم (الواقع الافتراضي/الواقع المعزز)
- تجارب غامرة: While distinct from physical models, VR allows users to virtually “خطوة إلى الداخل” the designed space at full scale. AR can overlay digital information onto a physical model. These technologies complement physical models by offering different ways to experience the design.
Presenting & Photographing Interior Models Effectively
Creating a great model is only half the battle; presenting it effectively, especially through photography, is crucial for conveying its message. Here are tips specifically for documenting interior models:
Use Natural Light When Possible
- Why: Natural light reveals forms and material textures most clearly and accurately.
- Tip: An overcast day often provides soft, even light with gentle shadows, which is ideal. Direct sunlight can create dramatic but potentially obscuring shadows. Avoid harsh desk lamps that create unnatural color casts.
Photograph at Perceived Human Height
- Why: Since interiors are experienced by people, photographing the model from a low angle, as if the camera lens is at eye level within the space, provides the most relatable and understandable perspective.
- Tip: Use your smartphone camera; its small size often allows you to place it *inside* the model to achieve realistic viewpoints. Avoid overly high, birdseye views unless specifically illustrating the overall layout.
Add Human Figures for Scale
- Why: Including scaled figures (cut-out sketches or purchased plastic figures) immediately gives viewers a sense of the model’s scale and the proportions of the space relative to people.
- Tip: This is especially helpful for abstract models or when the context isn’t immediately obvious.
Be Strategic with Color and Texture
- Why: Trying to perfectly represent every material and color can sometimes make the model look busy or like a dollhouse, distracting from the core spatial idea.
- Tip: Consider using color or texture strategically to highlight specific zones, material changes, or key forms. Sometimes a monochrome model focusing purely on form and layout can be very effective.
Document Abstract Models and the Process
- Abstract Models: Don’t forget to photograph conceptual or abstract models exploring form, نَسِيج, or assembly. Shoot from various angles.
- Process Shots: Documenting the step-by-step construction can showcase techniques, reveal internal structures, or highlight effective earlier iterations.
Shoot Variety and Don’t Fear Editing
- Variety: Photograph the same model from multiple angles (overhead, eye-level, detail shots), in different lighting conditions, and with different backgrounds or added elements. You never know which view will be needed.
- Editing/Annotation: Simple edits can improve photos (على سبيل المثال, converting a poorly lit color photo to black and white to focus on form). Annotations directly on the image (labels, notes, sketched figures) can add valuable context.
Combine Models with Other Media
- نموذج + رسم: Print photos and sketch design variations directly onto tracing paper overlays, using the photo’s perspective.
- رسم + نموذج: Add 3D elements directly onto copies of technical drawings (plans, أقسام) to explore interventions three-dimensionally.
- نموذج + Photoshop: Use image editing software to add realistic textures, entourage, or atmospheric effects to photographs of the physical model.
مواد & أدوات التجارة (مفصل)
Let’s revisit the essential materials and tools with a bit more detail on their specific uses in interior model making.
Common Materials Revisited
- Foam Board/Foamcore: Excellent for quick construction of walls and base structures. Easy to cut with a sharp knife. Different thicknesses available. Good for massing studies.
- Cardstock/Chipboard/Museum Board: Versatile for walls, الأرضيات, simple furniture. Can be scored and folded. Comes in various thicknesses and colors. Can be used to represent finishes.
- البلسا وود: Very lightweight, extremely easy to cut and carve. Ideal for detailed furniture, trim work, architectural details. Takes paint and stain well but is fragile.
- Basswood/Other Woods: Stronger than balsa, still relatively easy to work with. Good for more durable furniture, العناصر الهيكلية, الأرضيات. Can be laser cut.
- Styrene Sheets/Strips/Shapes: Plastic material available in various thicknesses and profiles. Cuts easily (score and snap). Excellent for fine details, window/door frames, modern furniture. Bonds well with plastic cement.
- الأكريليك (Plexiglass): Rigid, clear plastic perfect for representing glass windows, partitions, display cases, or even water features. Requires specialized cutting tools (scoring knife, saw) or laser cutting.
- 3D Printing Filaments/Resins: جيش التحرير الشعبى الصينى, ABS, PETG filaments for FDM printers (good for structural parts, larger furniture). Photopolymer resins for SLA/DLP printers (essential for high-detail miniatures, complex shapes).
- Fabrics/Textiles: Small pieces of actual fabric or thin materials to simulate upholstery, curtains, rugs. Scale texture is important.
- الدهانات & Finishes: Acrylic paints are versatile. Spray paints for even coverage. Specific model paints (المينا, lacquers). Varnishes (matte, satin, gloss) to simulate different surface sheens. Texturing paints or mediums.
- مواد لاصقة: PVA glue (wood/paper), plastic cement (styrene), CA glue (super glue – quick bonds, various viscosities), epoxy (strong bonds), spray adhesive (large flat surfaces).
Essential Tools Revisited
- Cutting Mat: Self-healing type protects surfaces and preserves blade sharpness.
- Knives: Sharp craft knives (X-Acto style #11 blades are standard), utility knives for heavier materials, scoring knives for acrylic. Frequent blade changes are key to clean cuts.
- Rulers/Squares: Metal rulers with cork backing (prevents slipping), scale rulers, small engineer’s squares, combination squares for accuracy.
- Measuring Devices: Calipers (digital or dial) for precise measurements, flexible measuring tape.
- Sanding Tools: Sanding blocks, sanding sticks, various grits of sandpaper, small files for shaping and smoothing edges.
- Clamps/Tweezers: Small clamps, spring clamps, tweezers (various types – pointed, flat, reverse action) for holding parts while gluing or positioning.
- Safety Gear: Safety glasses are essential when cutting or using power tools. Dust mask when sanding. Good ventilation when painting or using strong adhesives.
- Optional Power Tools: Small scroll saw, mini table saw, Dremel rotary tool (for grinding, polishing, cutting), laser cutter, 3D printer.
Common Challenges & Solutions in Interior Model Making
Creating detailed interior models comes with its own set of specific challenges. Here’s a look at common hurdles and how experienced model makers overcome them.
تحدي: Achieving Detail at Small Scale
- The Issue: Replicating intricate furniture details, المباريات, or decorative patterns accurately when everything is miniaturized. Features can become too small to physically create or appear crude.
- Solutions: Use high-resolution fabrication methods like SLA/DLP 3D printing. Employ fine tools and magnification. Simplify non-essential details strategically. Focus on conveying the *impression* of detail rather than exact replication sometimes. Choose an appropriate (often larger) scale for highly detailed projects.
تحدي: Realistic Material Representation
- The Issue: It’s difficult to find miniature materials that perfectly mimic the texture, sheen, and grain of full-scale materials like wood, حجر, قماش, أو المعدن. Applying finishes consistently can also be tricky.
- Solutions: Skillful painting and texturing techniques are key (dry brushing, washes, stippling). Use actual material samples where feasible (thin wood veneers, fine fabrics). Print high-resolution textures onto paper or decal film to apply to surfaces. Select materials carefully based on how well they simulate the real thing at scale.
تحدي: Color Accuracy and Lighting Representation
- The Issue: Colors can appear different under model lighting or at a smaller scale. Accurately simulating the quality and effect of both natural and artificial light within the model is complex.
- Solutions: Use color swatches and test paints under the intended display lighting. Understand color theory and how scale affects perception. Plan lighting integration carefully, using appropriate miniature LEDs and diffusers. Consider building small lighting mock-ups.
تحدي: Balancing Durability with Fine Details
- The Issue: Highly detailed models with delicate parts (thin furniture legs, small accessories) can be very fragile and easily damaged during handling or transport.
- Solutions: Use stronger materials for structural elements (على سبيل المثال, acrylic instead of cardstock). Design connections carefully. Consider slightly thickening very fine parts if possible without compromising aesthetics. Provide a sturdy base and a protective acrylic cover. Advise clients on proper handling procedures.
تحدي: Maintaining Spatial Accuracy and Scale Consistency
- The Issue: Ensuring all elements – walls, أثاث, fixtures – are consistently and accurately scaled relative to each other. Even small errors can distort the perception of the space.
- Solutions: Work meticulously from accurate plans and measurements. Use precise cutting and measuring tools. Double-check scales frequently during construction. Employ CAD and automated fabrication (laser, 3D print) where possible for consistent part sizing.
Overcoming these challenges requires a combination of technical skill, artistic sensibility, patience, and careful planning.
Understanding the Costs of Interior Models
The investment required for an interior model varies widely. Several factors influence the final price:
Key Factors Influencing Cost
- Size and Scale: Larger models naturally require more materials and labor. Larger scales (على سبيل المثال, 1:10 vs 1:50) allow for more detail but also increase complexity and material usage.
- Level of Detail and Complexity: Highly detailed models with intricate furniture, custom fixtures, complex geometry, and realistic finishes take significantly more time and skill to create.
- التفاعل: Adding functional lighting, أجزاء متحركة, or other interactive elements increases cost due to components and specialized labor.
- المواد المستخدمة: High-quality materials like acrylic, certain woods, المعادن, or specialized 3D printing resins are more expensive than basic foam board or cardboard.
- Fabrication Techniques: Extensive use of 3D printing or CNC machining can impact cost compared to simpler hand-cutting methods (though may save time).
- Labor and Expertise: The time and skill level of the model makers are major cost drivers. Complex projects require experienced artisans.
- Timeline: Rush jobs requiring overtime will typically incur higher costs.
- Design Changes: Significant changes requested after construction has begun can lead to additional costs.
- Base and Protective Casing: A custom display base and acrylic cover add to the overall cost.
Example Cost Ranges
Article 4 provides some specific (though potentially indicative) cost estimates. It’s crucial to get custom quotes, but these offer a general idea:
Model Type / Scope | Estimated Cost Range (USD) | Estimated Cost Range (EUR approx.) | Estimated Cost Range (GBP approx.) |
---|---|---|---|
Simple DIY House Model (Basic Rooms) | $300 – $500 | €270 – €450 | £230 – £385 |
Finished DIY House Model (Higher Grade) | $800 – $1,500 | €720 – €1,350 | £615 – £1,150 |
Professional House Model (مفصل) | $2,000 – $3,000+ | €1,800 – €2,700+ | £1,540 – £2,300+ |
Basic DIY Living Room Model | $50 – $100 | €45 – €90 | £38 – £77 |
Mid-Range DIY Living Room Model | $300 – $500 | €270 – €450 | £230 – £385 |
Professional Living Room Model | $1,000 – $2,000+ | €900 – €1,800+ | £770 – £1,540+ |
Basic DIY Bathroom Model | $50 – $75 | €45 – €68 | £38 – £58 |
Realistic DIY Bathroom Model | $200 – $300 | €180 – €270 | £153 – £230 |
Professional Bathroom Model | $1,000 – $1,500+ | €900 – €1,350+ | £770 – £1,150+ |
Basic DIY Kitchen Model | $100 – $150 | €90 – €135 | £77 – £115 |
Realistic DIY Kitchen Model | $300 – $500 | €270 – €450 | £230 – £385 |
Professional Kitchen Model | $1,500 – $2,000+ | €1,350 – €1,800+ | £1,150 – £1,540+ |
General Professional Range | $1,000 – $250,000+ | €900 – €225,000+ | £750 – £190,000+ |
Note: These are illustrative ranges based on one source. Actual costs will vary significantly based on the factors listed above. The large general range reflects the vast difference between simple massing models and extremely high-end, detailed presentation models.
DIY vs. Professional
As the table shows, DIY models can be significantly cheaper in terms of material cost but require substantial time, مهارة, and tools. Professional models command higher prices but offer expertise, access to advanced technology, higher quality finishes, and save the client’s time.
Software Used in Interior Modeling
While physical models are the focus, digital tools play a crucial role in their design and often in generating components for fabrication. Common software includes:
- سكيتش اب: Popular for its intuitive interface and ease of creating 3D forms quickly. Widely used for conceptual and schematic interior modeling. Large component library (3D Warehouse).
- أوتوكاد: Industry standard for precise 2D drafting (floor plans, الارتفاعات) and also offers robust 3D modeling capabilities, especially for architectural elements.
- ريفيت: نمذجة معلومات البناء (بيم) برمجة. Creates intelligent, data-rich models where components have associated information. Excellent for integrated design including MEP systems.
- 3س ماكس: Strong in detailed modeling, النسيج, and especially high-end, photorealistic rendering of interior scenes. Often used for visualization alongside physical models.
- وحيد القرن (Rhinoceros 3D): Powerful freeform NURBS modeling software, excellent for creating complex curves and custom furniture shapes with high precision.
- Adobe Photoshop: Used for creating or editing textures, post-processing renderings, or adding annotations/graphics to photos of physical models. Interior Model Making
The craft continues to evolve, blending tradition with innovation:
- Digital Integration (الواقع الافتراضي/الواقع المعزز): Expect more seamless integration between physical models and digital overlays or immersive virtual experiences.
- Advanced Materials & 3د الطباعة: Continued development of materials that offer greater realism, متانة, or unique properties. More sophisticated multi-material and full-color 3D printing.
- التركيز على الاستدامة: Increased use of eco-friendly, recycled, or biodegradable materials and more resource-efficient fabrication processes.
- Hyper-Personalization: Technology like 3D scanning and printing makes it easier to create highly customized models, perhaps even replicating a client’s existing furniture in miniature.
- Data-Driven Design Input: Potential for models to be informed by or interact with data analytics regarding space utilization or environmental performance.
- Enhanced Collaboration Tools: Digital platforms facilitating easier collaboration around both digital and physical model reviews.
Choosing the Right Interior Model Maker
Finding the right partner is key to getting a model that truly serves its purpose. Consider these factors:
- Specialization in Interiors: Look for a maker with demonstrated experience and understanding of interior spaces, أثاث, وينتهي, not just exterior architecture.
- جودة الحافظة: Critically assess their past interior work. Does it show the level of detail, realism, and craftsmanship you require?
- Technical Capabilities: Do they possess the necessary tools and technologies (high-res 3D printing, القطع بالليزر, finishing expertise) for your project’s complexity?
- Understanding of Design Intent: Can they grasp and translate your specific design aesthetic, material choices, and desired ambiance?
- Communication and Process: Do they have a clear communication process? How do they handle feedback and revisions?
- Material Expertise: Do they demonstrate knowledge in selecting and simulating a wide range of interior materials convincingly?
- Attention to Detail: Is meticulousness evident in their work? Interiors often live or die by the details.
- References and Reputation: Check reviews or ask for client references if possible.
خاتمة: The Enduring Value of Seeing Inside
In the complex world of architecture and interior design, the ability to clearly visualize and communicate spatial ideas is paramount. Interior models provide an unparalleled solution, transforming abstract plans into tangible realities that can be explored, evaluated, and refined.
They bridge communication gaps, empower clients, reduce costly errors, and serve as powerful marketing assets. While digital tools offer incredible capabilities, the physical interior model retains a unique power to engage the senses, foster intuitive understanding, and build confidence in a design. By combining skilled craftsmanship with appropriate technology, interior models effectively bring proposed spaces to life, ensuring that the final built environment truly meets the vision and needs of its users. They are not just representations; they are essential instruments for achieving design excellence.
الأسئلة المتداولة (FAQs) About Interior Models
Here are answers to common questions regarding interior models:
- What materials are typically used for architectural interior models?
- Common materials include foam board, كرتون, various woods (like balsa or basswood), البلاستيك (styrene, أكريليك), 3D printed resins/plastics, fabric samples, and specialized paints and finishes.
- How do interior models help in client presentations?
- They provide a tangible, 3D view that clients can easily understand, interact with, and relate to, making discussions more productive and decisions more confident compared to relying solely on drawings or digital images.
- Can interior models be created digitally instead of physically?
- نعم, digital 3D modeling is very common using software like SketchUp or Revit. لكن, physical models offer unique benefits in tactile exploration and immediate spatial understanding that digital models can lack.
- How can interior models contribute to sustainable design?
- Models can help visualize and evaluate aspects like natural light penetration, ventilation paths, and the placement of sustainable materials, aiding architects in optimizing designs for energy efficiency and environmental performance.
- Are interior models only used for new construction projects?
- لا, they are also very useful for renovation, restoration, and alteration projects to help visualize proposed changes and improvements within existing spaces.
- What scale is best for an interior model?
- Scales typically range from 1:10 ل 1:50 to allow for sufficient detail in furniture and finishes. The choice depends on the project size and the level of detail required.
- How much does an interior model cost?
- Costs vary widely based on size, التفاصيل, مواد, interactivity, and labor. It can range from under $100 for a simple DIY model to hundreds of thousands for large, hyper-realistic professional presentation models. Custom quotes are essential.
- What kind of architect typically creates interior models?
- While many architects create basic models, specialized *Interior Architects* or dedicated architectural model making firms often have the specific skills and focus required for high-quality, نماذج داخلية مفصلة
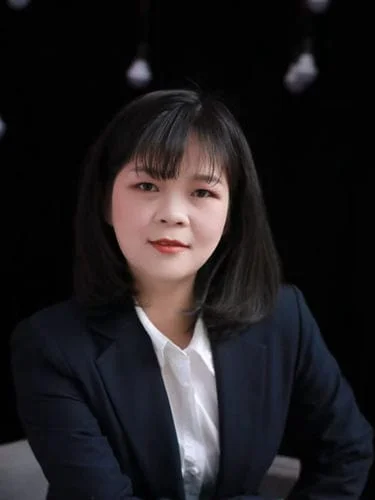