Architectural model making is a crucial skill for anyone involved in the world of design and construction. Whether you’re a student, a seasoned pro, or just a hobbyist, crafting a well-made model can be a game-changer. It’s like bringing your blueprints to life! These miniature structures do more than just look cool – they help you spot potential problems, show off your design to clients, and even help secure funding for your projects. Think of it like this: a picture might be worth a thousand words, but a model is worth a million.
This guide is packed with practical tips and tricks to help you up your model-making game. We’ll walk through everything from the initial planning stages to those final, detalles intrincados. Más, we’ll look at some cool advanced techniques for when you’re ready to take things to the next level. No matter where you are in your architectural journey, this guide has something for you.
Tabla de contenido
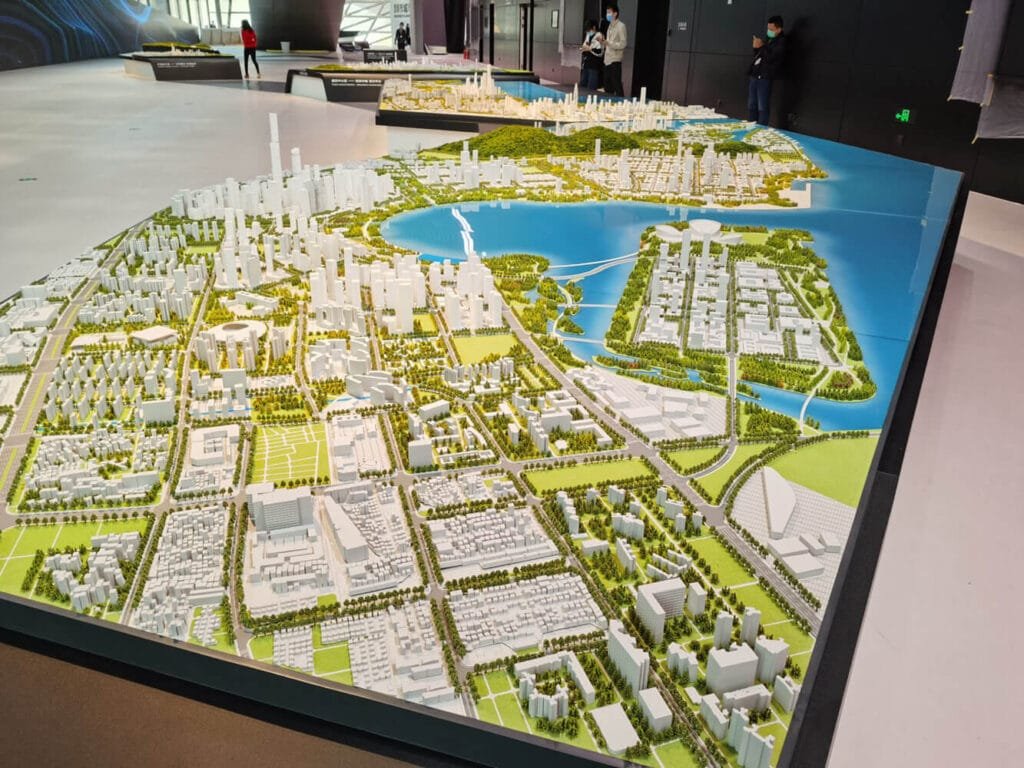
Planning and Preparation
Defining the Purpose and Scope
1. Understand the Model's Objective:
Are you trying to explore a concept, refine a design, or wow a client? Maybe you’re trying to secure funding or get the public excited about a new project. Each of these objectives calls for a different approach to model making. Piense en ello: a model for a quick brainstorming session will look very different from one you’d present to a potential investor.
- Conceptual exploration: Keep it simple and flexible.
- Design development: Focus on specific design elements and how they work together.
- Client presentation: Aim for a polished, detailed model that showcases the project’s best features.
- Marketing: Create a visually stunning model that captures attention and generates interest.
2. Determine the Level of Detail:
How intricate should your model be? The answer depends on what you’re using it for. A conceptual model can be pretty basic, while a presentation model needs to show off all the bells and whistles. If you’re building a model to show off to clients, you’ll want to include more details, like tiny furniture or landscaping. But if it’s just for you to test out ideas, you can keep it simple.
3. Consider the Audience:
Choosing the Right Scale
1. Understand Scale Ratios:
Architectural models use different scales, como 1:10, 1:50, o incluso 1:500 for urban planning models. What does that mean? Bien, a 1:10 scale means that every inch on your model represents 10 inches in real life. Each scale has its own purpose. If you are modelling a single room, 1:10 o 1:25 might be best. For a house, maybe you want 1:50 o 1:100. For a whole city block? You might go as small as 1:500 o incluso 1:2500.
Here’s a quick look at common scales:
Escala | Uso típico |
---|---|
1:10 | Interior details, muebles |
1:25 | Interior room layouts |
1:50 | Single-family homes, small buildings |
1:100 | Larger buildings, small complexes |
1:200 | High-rises, larger complexes |
1:500 | City blocks, urban planning |
1:2500 | Large-scale urban planning, regional models |
2. Select the Appropriate Scale:
Creating a Time Plan and Budget
1. Develop a Realistic Schedule:
2. Estimate Material Costs:
3. Prioritize Key Features:
If you’re on a tight budget or up against a deadline, you might not be able to do everything you want. That’s okay! Just focus on the most important parts of the design. What are the key features that really sell your idea? Maybe it’s a unique roofline or a cool interior courtyard. Whatever it is, make sure those elements shine in your model. You can always add more details later if you have time and money.
Gather Design Drawings and References
1. Use Accurate Plans and Elevations:
This is super important. You need to print out your architectural drawings to the right scale. These will be your templates, so accuracy is key. And make sure you have a few copies on hand. You never know when you might need a backup. A good tip is to print out extra copies of your plans. That way, you can cut them up and use them as templates without worrying about messing up your original drawings.
2. Utilize Digital Models:
Selección de material
Choosing Materials Based on Model Type and Purpose
1. Modelos conceptuales:
2. Modelos de trabajo:
3. Modelos de presentación:
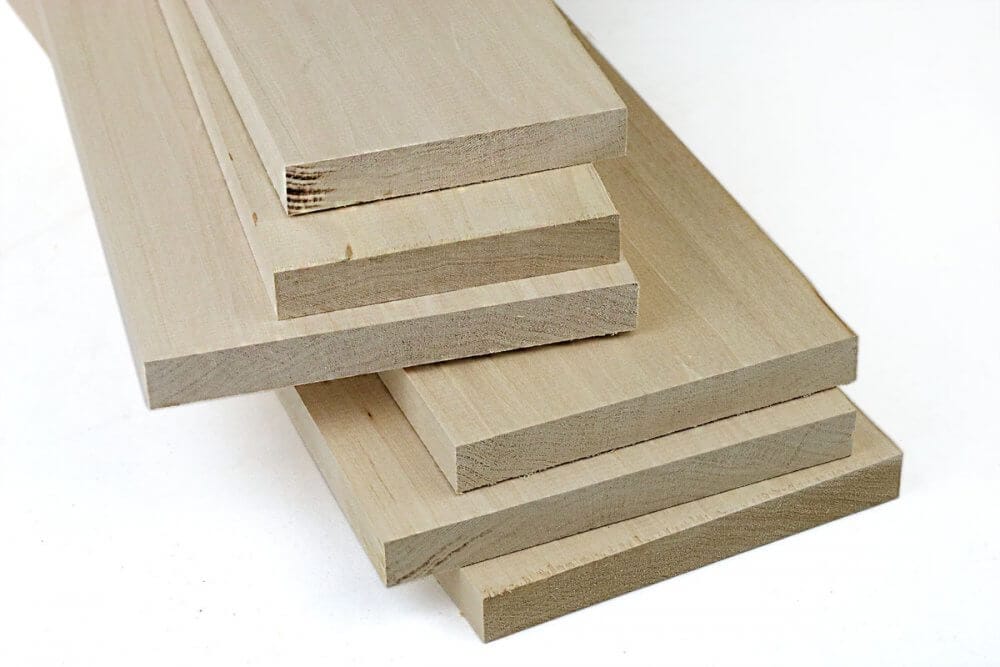
Exploring Different Material Options
1. Paper and Cardboard:
These are your go-to’s for quick and easy models. Card stock is great for its flexibility and comes in different colors. Chipboard is thicker and good for sturdy structures. Kraft board is super strong and perfect for larger models.
Here is a table about Paper and Cardboard:
Material | Descripción | El mejor uso |
---|---|---|
Card Stock | Flexible, comes in various colors, thicker than regular paper | Modelos rápidos, curved surfaces |
Chipboard | Thicker than card stock, sturdy, often comes in two or three sheets (duplex or triplex) | Structural elements, base models |
Kraft Board | Very strong, rigid, can be cut cleanly | Large-scale models, durable structures |
Cartulina | Ligero, recyclable, uniquely flexible | Adding light details like roads, pathways, terrains |
2. Madera:
Wood brings a natural, warm feel to your models. Balsa wood is a favorite because it’s lightweight and easy to cut. Basswood is denser and has a finer grain, making it good for detailed work. MDF is heavy and best for bases. Balsa is so easy to work with; you can even cut it with a craft knife!
Here is a table about Wood:
Material | Descripción | El mejor uso |
---|---|---|
Madera de balsa | Ligero, fácil de cortar, comes in panels or thin strips | Framework, detailed structures, can be cut by hand or laser cut |
Bosque | Denser and heavier than balsa, fine grain | Detailed work, strip wood with a fine grain |
MDF (Medium-density Fiberboard) | Thick, dense, heavy, good finish | Model bases, large architectural models |
Cork | Natural finish, flexible but breakable | Modeling hilly sites, can be layered for terrains |
3. Espuma:
Foam is fantastic for quick massing models. Foam board comes in different thicknesses and colors and is super easy to cut. Insulation board, also known as blue foam, is great for conceptual models. Gator board is a bit fancier – it’s lightweight but also moisture-resistant.
Here is a table about Foam:
Material | Descripción | El mejor uso |
---|---|---|
Foam Board | Ligero, comes in various thicknesses and colors, smooth finish | Massing models, paredes, bases |
Insulation Board (Blue Foam) | Ligero, easy to model with, comes in various colors (blue, gray, pink, brown) | Conceptual models, site models (brown foam) |
Gator Board | Ligero, smooth finish, moisture-resistant | High-quality models, presentations |
4. Plástica:
Plastics offer a clean, modern look. Acrylic sheets are perfect for windows and facades because of their glossy finish. ABS is super durable and great for laser cutting. PVC sheets are good for representing transparent elements. Acrylic is a bit trickier to work with, but the results are worth it!
Here is a table about Plastics:
Material | Descripción | El mejor uso |
---|---|---|
Sábanas acrílicas | Smooth, glossy finish, comes in various thicknesses | Windows, facades, modern-looking models |
ABS (Acrylonitrile Butadiene Styrene) | Durable, dissolves in acetone, fuses together neatly | Laser-cut models, detailed parts |
PVC Sheets | Rigid, used to represent transparent and translucent parts | Windows, transparent elements |
5. Metal:
6. Clay and Plasticine:
Considering Material Properties
1. Durability and Longevity:
2. Ease of Cutting and Shaping:
3. Surface Finish and Texture:
4. Compatibility with Adhesives and Paints:
Using Premade Architectural Model Materials
1. Landscaping Elements:
2. Figures and Vehicles:
3. Furniture and Fixtures:
Tool Selection and Usage
Essential Cutting Tools
1. Cutting Knives:
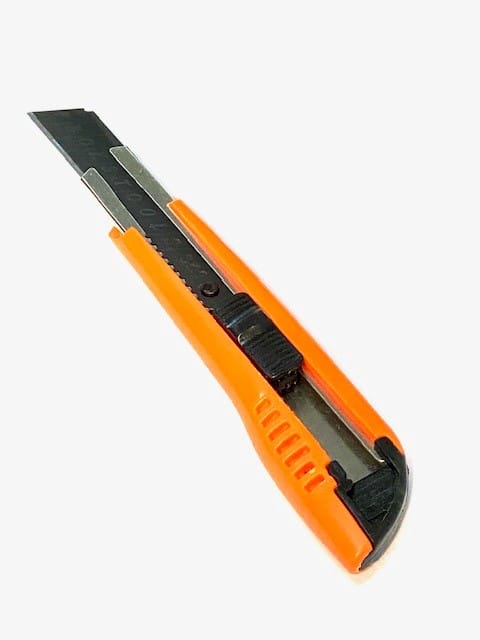
These are your workhorses. You’ll be using them for everything from scoring foam board to cutting intricate details. The Olfa 9mm knife is a great all-around choice. It has an adjustable blade, so you can use just the tip for fine details or extend it for thicker materials. The X-Acto knife is perfect for super precise cuts. But be warned, they are extremely sharp!
Here’s a tip: always use a fresh blade. A dull blade is more dangerous than a sharp one because you have to use more force, which can lead to slips and accidents and always cut away from yourself and keep your fingers clear of the blade’s path.
2. Scissors:
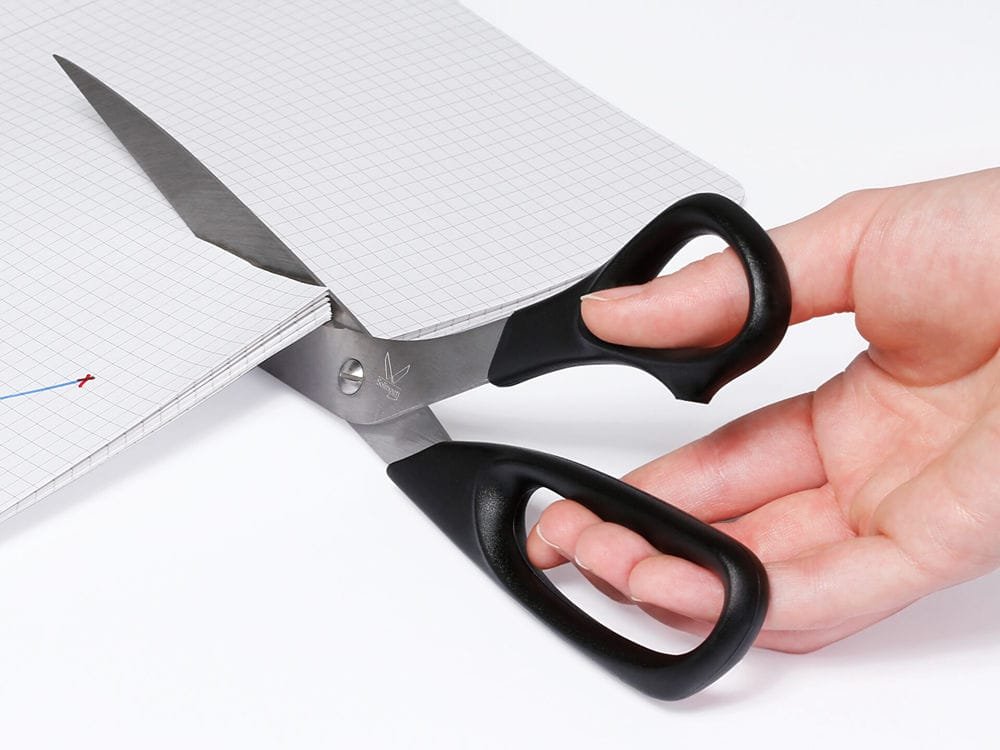
3. Metal Rulers:
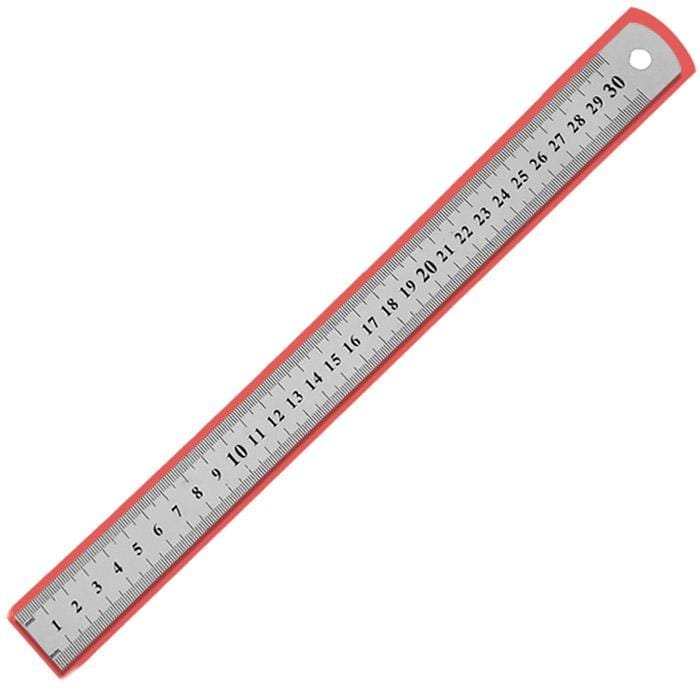
4. L-Squares:
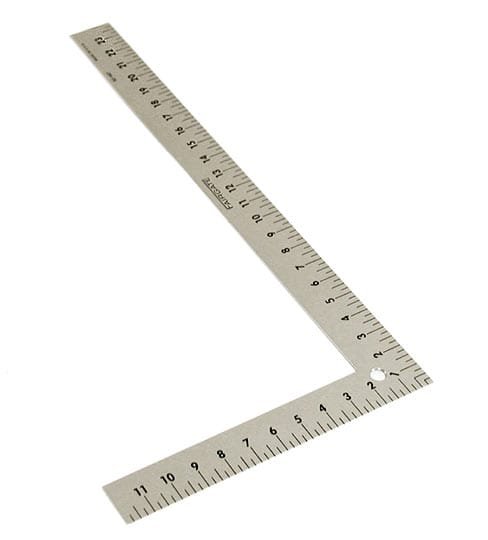
5. Self-Healing Cutting Mats:
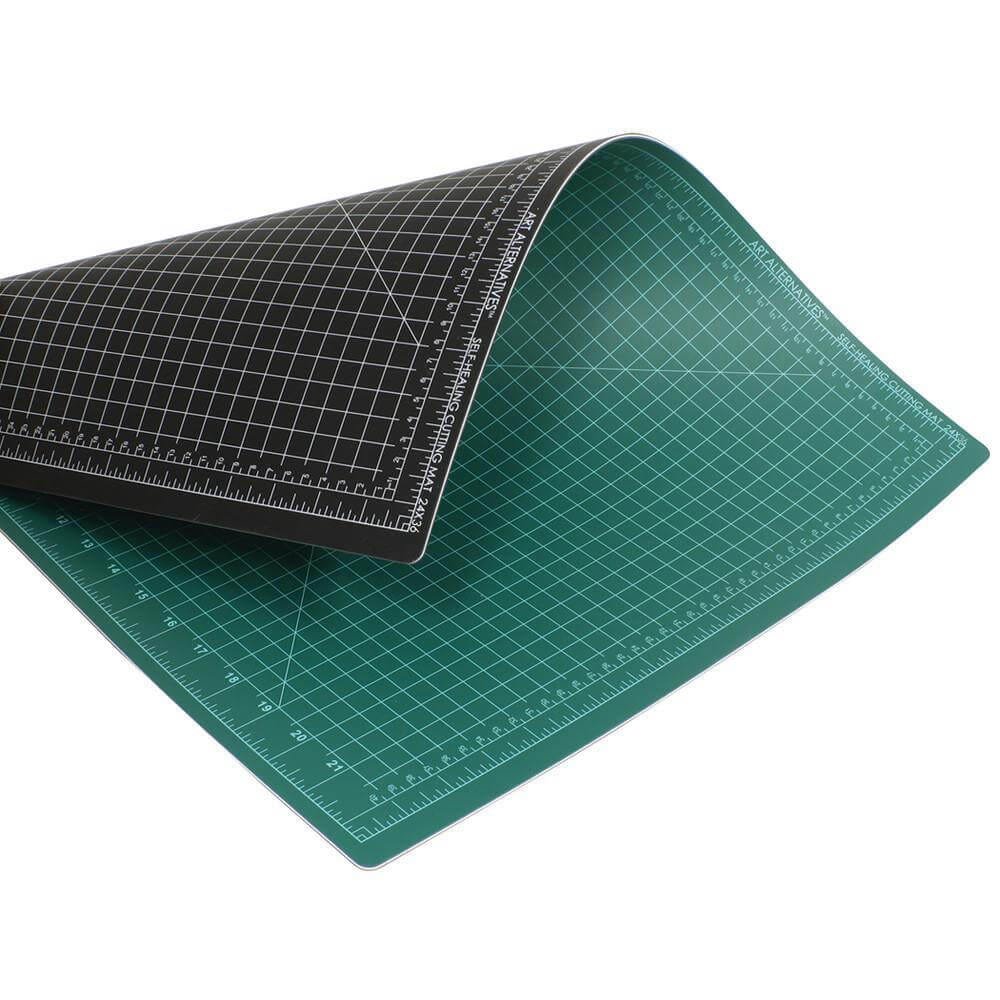
Assembly Tools and Adhesives
1. Glue Selection:
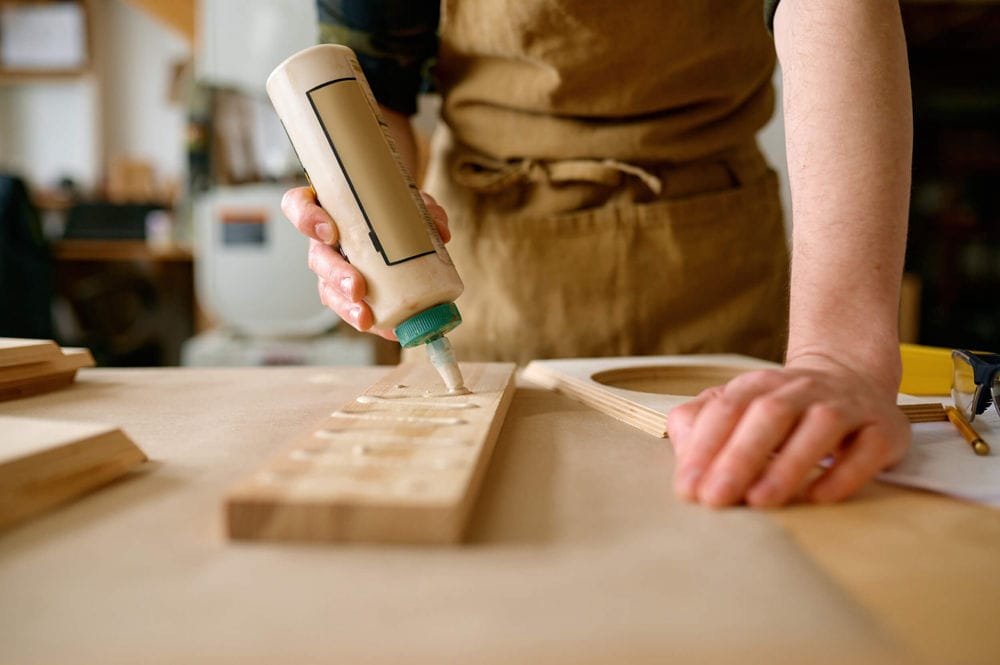
Choosing the right glue is crucial. Here’s a quick rundown:
Here’s a quick look at common glue:
Glue Type | Descripción | Mejor para |
---|---|---|
Glue Sticks | Cheap, fácil de usar, not very strong | Temporary bonding, paper |
White Glue | Non-toxic, general purpose, dries clear | Paper, cartulina, madera (light-duty) |
Tacky Glue | Thicker than white glue, stronger, faster drying | Most materials, general model making |
Hot Glue | Fastest drying, strong bond, can be messy | Quick fixes, attaching landscaping elements |
Wood Glue | Specifically for wood, strong bond, stains if not cleaned | Wood models, structural elements |
Glue Sticks: These are okay for quick fixes or sticking paper together, but they’re not very strong.
White Glue: This is your basic, all-purpose glue. It works on lots of materials, but it takes a while to dry.
Tacky Glue: This is like white glue but stronger and faster drying. It’s a good all-around choice for model making.
Hot Glue: This stuff dries super fast, which can be good and bad. It’s great for quick fixes, but you have to work fast. Be careful, though – it’s hot! I’ve burned myself more times than I care to admit.
Wood Glue: If you’re working with wood, you need wood glue. It creates a super strong bond.
2. Glue Application:
3. Double-Sided Tape:
4. Tweezers:
Other Useful Tools
1. Sandpaper:
2. Modeling Pliers:
3. Dusting Brush:
4. Acrylic Cutting Tool
Construction Techniques and Tips
Cutting Techniques
1. Scoring and Snapping:
2. Using Templates:
3. Cutting Order:
4. Maintaining Sharp Blades:
Assembly Techniques
1. Dry Fitting:
2. Gluing Strategies:
3. Layering and Reinforcement:
4. Adding Texture and Color:
2. Creating Windows and Doors:
For windows, use clear plastic sheets. You can buy these at most craft stores or online. Cut them to size and glue them in place. For doors, you can use the same material as your walls, or you can use something different to make them stand out. You can even add tiny details like doorknobs or hinges to make them look more realistic.
Here’s a tip: If you’re modeling a building with lots of windows, create a template for the window openings. This will ensure that all your windows are the same size and shape.
3. Incorporating Landscaping:
4. Adding Figures and Vehicles:
Advanced Techniques
Corte con láser
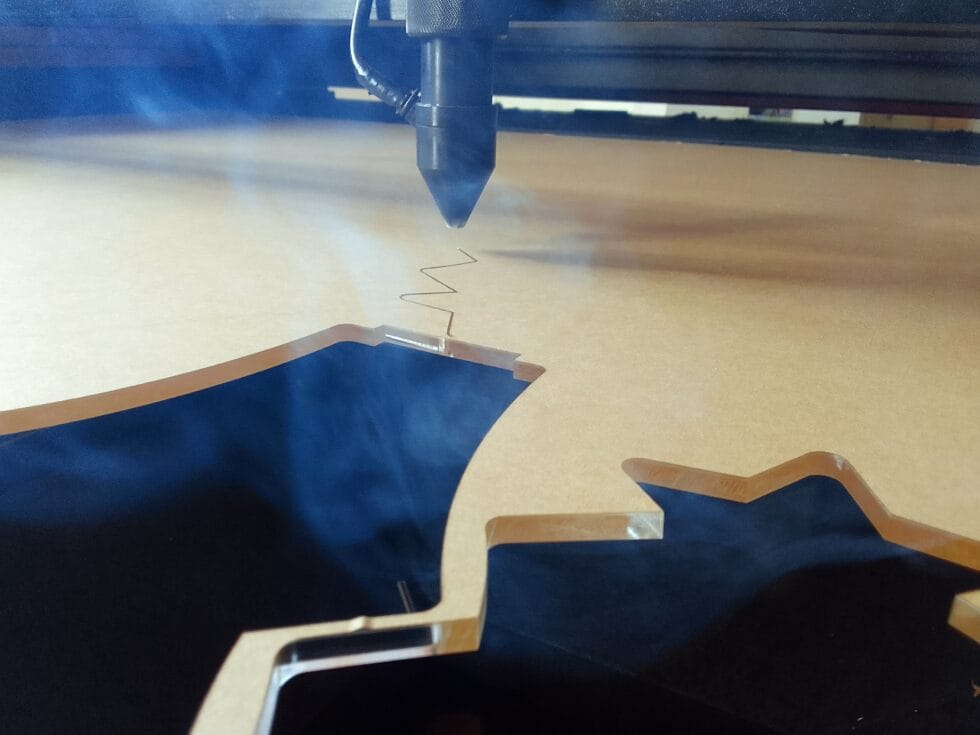
Laser cutting is a great way to create precise, intricate parts. It’s especially useful for cutting thin materials like acrylic, madera, and some plastics.
Here’s a tip: If you’re using a laser cutter, always make sure the settings are correct for the material you’re using. Using the wrong settings can damage the material or even start a fire.
1. Preparing Files:
2. Material Considerations:
3D impresión
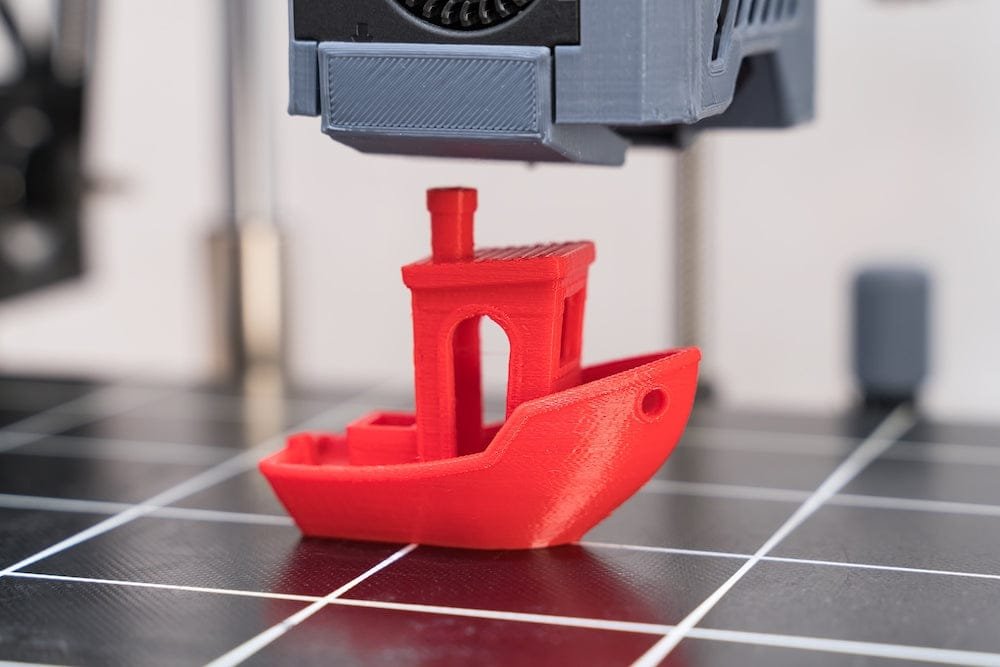
1. Model Preparation:
To 3D print a part, you’ll need a 3D model. You can create one in programs like Blender, Bosquejo, or Tinkercad. Make sure your model is “estanco,” meaning it doesn’t have any holes or gaps. There are lots of free 3D modeling software options available online. You can also find pre-made 3D models online that you can use in your projects.
2. Material Options:
Presentation and Maintenance
Creating a Base
1. Choosing Materials:
2. Finishing the Base:
3. Adding Context:
Lighting
Lighting can make a huge difference in how your model looks. It can highlight certain features, create shadows, and add drama. This can really help to showcase your design and make it more engaging.
1. Mejorar el realismo:
2. Types of Lighting:
Photography
1. Using a Simple Background:
2. Proper Lighting:
3. Camera Settings:
Maintenance
1. Cleaning:
2. Storage:
3. Protection
Conclusión
Model making is a journey, not a destination. It takes time, patience, and practice. But with the right planning, materiales, tools, and techniques, you can create amazing models that bring your designs to life. Don’t be afraid to experiment and try new things. And most importantly, have fun! Recordar, every model you build is a learning experience.
Ready to take your model-making skills to the next level? Start your next project today! Explore our website to dive deeper into related topics, like architectural drawing techniques, the best architecture software, architecture design competitions, parametric design, or even urban design best practices. You can find links to suppliers, manufacturers, and other helpful resources.
Q&A Section
Let’s tackle some common questions about architectural model making:
Q: What is the purpose of architectural model making?
A: It’s all about bringing designs to life! Models help architects explore ideas, refine designs, and communicate concepts to clients and the public. They’re also used for marketing, securing funding, and even as presentation tools.
Q: What scale is used in most architectural models?
A: It depends on the project, but common scales range from 1:10 for detailed interiors to 1:500 o 1:2500 for urban planning. Smaller scales are used for larger projects.
Q: What are the suitable materials to use in an architectural model?
A: The best material depends on the type of model and your budget. Espuma, cartulina, and paper are great for conceptual models. Madera, acrílico, and high-quality foam board are good for presentation models. There are tons of options, from balsa wood and basswood to acrylic sheets and PVC.
Q: What are the right tools to use for cutting and assembly in model making?
A: You’ll need cutting knives (Olfa 9mm, X-Acto), scissors, metal rulers, L-squares, a self-healing cutting mat, and various glues (white glue, tacky glue, hot glue, wood glue). Tweezers and a drafting brush are also super helpful.
Q: How do you make a good architectural model?
A: Plan carefully, choose the right scale and materials, use sharp tools, and take your time. Practice makes perfect! Presta atención a los detalles, use templates for repeated elements, and don’t be afraid to experiment.
Q: How do you present an architectural model?
A: Create a sturdy base, consider the context, and use lighting to your advantage. Make sure the model is clean and well-maintained. Think about the story you want to tell with your model.
Q: How do you photograph architectural models?
A: Use a simple background, good lighting (natural or artificial), and a tripod. Adjust your camera settings for optimal focus and depth of field. Take photos from multiple angles.
Q: How do I plan an architectural model?
A: Define your objective, choose the right scale, create a schedule and budget, and gather all necessary drawings and references. Think about your audience and the level of detail needed.
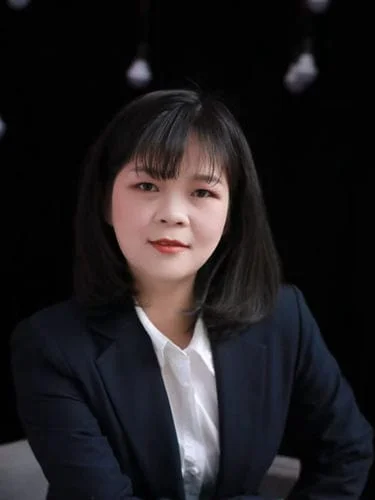