In architectural model-making, selecting the right material is crucial for achieving the desired outcome at each stage of the design process. From conceptual models using affordable materials like foam board and cardboard to presentation models requiring more refined options like acrylic and wood, material choice affects durability, precision, and aesthetic appeal. Eco-friendly materials like recycled plastics and biodegradable foams are gaining traction for sustainable designs. Understanding how to handle, cut, and bond these materials, along with avoiding common mistakes, will help elevate your models. Experimentation and flexibility with materials can enhance both design expression and model quality.
Table of Contents
The Importance of Material Selection in Architectural Models
Materials: The Foundation of Every Architectural Model
When it comes to architectural models, materials are far more than just “stuff” to build with. They’re the unsung heroes of the design process, shaping how a concept is perceived, understood, and experienced. The right material can transform a simple sketch into a tangible piece of art, bringing out the soul of a design and helping it leap off the page (or the screen, or the drafting table) and into the real world. Without the proper materials, even the most brilliant architectural ideas can fall flat—just like trying to build a house on a foundation of quicksand.
Why does material selection matter? Well, imagine trying to convey the sleek, modern lines of a high-rise with something that looks and feels like cardboard. Not quite the message you’re aiming for, right? Materials do more than represent the physical characteristics of a building—they help express the scale, form, texture, and design intent behind the structure. Materials bring your vision to life and help others understand the dream you’re trying to communicate.
The right materials can also define the mood and emotion of your model. Whether you’re using the smooth, transparent finish of acrylic to convey modernity or the earthy, natural feel of wood to evoke warmth and sustainability, each material choice sends a message about the design. And beyond aesthetics, materials also play a crucial role in functionality—helping to test out structural ideas, demonstrate proportions, and ensure that the final product is just as solid as the vision behind it.
Purpose of the Article: Your Ultimate Guide to Material Selection
So, why are we here today talking about architectural model materials? The answer is simple: choosing the right material is like choosing the right color palette for a painting. It’s all about communicating the right message, in the right way, at the right time. Whether you’re working on a conceptual model that tests out new ideas or a final presentation model that will be used to woo clients, the materials you choose will directly affect how your design is perceived.
In this article, we’ll help guide you through the labyrinth of materials available for architectural model-making. You’ll learn which materials are best suited for different stages of the design process, from early conceptual sketches to refined, detailed presentations. Along the way, we’ll explore the benefits and drawbacks of various materials—whether you’re aiming for something cost-effective, durable, or visually stunning.
By the time you finish reading, you’ll have a solid understanding of how to select the perfect materials based on your project’s specific needs, whether it’s for design exploration, client engagement, or final presentation. Ready to dive in? Let’s get started!
Key Factors to Consider When Choosing Materials for Architectural Models
The Project Stage: From Concept to Reality
Choosing the right material for your architectural model is like picking the right outfit for a big event—it all depends on the occasion. The stage of your project determines whether you need something quick and conceptual or something that can survive scrutiny under a spotlight.
For a conceptual model, you’re not necessarily looking for perfect finishes—you’re exploring basic shapes, volume, and spatial relationships. Foam boards, cardboard, and paper are your go-to materials here—lightweight, inexpensive, and easy to manipulate. The idea is to get the concept across, not stress about the fine details.
But when you move into working models, where the design is more refined and needs to test out functionality and proportion, materials need to step it up. Think basswood, balsa wood, and acrylic. These materials are ideal for more intricate details and give you the durability you need for testing without sacrificing too much time or cost.
Then, there’s the final presentation model. This is where your design will be showcased in all its glory—so it needs to shine. Materials like acrylic, resin, or metal are perfect for this stage. You need precision, clean finishes, and durability to withstand handling while also providing that “wow” factor when it hits the boardroom or display table.
Budget Constraints: Building Dreams on a Budget
Ah, the eternal dilemma of every architect: trying to make your vision come to life without breaking the bank. Budget constraints are a big factor when selecting materials. If you’re working on a conceptual model, the budget might be tight—and that’s okay! Materials like cardboard, foam board, and paper are affordable and versatile, perfect for brainstorming and quick sketches. These materials do the job without the hefty price tag.
When you get into more detailed or working models, costs can start to rise, especially when using high-end materials like wood, resin, or acrylic. But these materials allow for more intricate detail and durability. The trick here is to balance functionality with cost-effectiveness—use pricier materials where they matter most and opt for budget-friendly options where they won’t be the star of the show.
For large-scale or long-term projects, planning is key. Recycled materials can be an eco-friendly (and cost-effective) choice. Materials like reclaimed wood or recycled plastics can provide strength and durability without inflating your budget. Sometimes, it’s not just about the materials you choose, but how creatively you can use them.
Time Requirements: Racing the Clock
Time is money—especially in the world of architectural model making. How quickly you need to produce your model will directly impact the materials you choose. If you’re in a time crunch and need a conceptual model fast, stick with materials that are easy to manipulate and require minimal effort to assemble. Materials like cardboard, foam board, or paper will allow you to knock out rough ideas without getting bogged down in the details. The focus is on speed, not perfection.
For more detailed models or presentation models, the timeline is likely longer, and that’s where acrylic, wood, or resin come into play. These materials require more time to work with, especially for sanding, cutting, and finishing, but the result is a model that stands up to scrutiny. In this case, the time spent is worth the added durability and visual impact. Laser cutting and 3D printing can help speed up processes, especially when it comes to precision cuts or intricate detailing.
Design Intent: What’s the Big Idea?
What’s your design’s story? Is it a futuristic skyscraper with sleek glass facades, or a rustic countryside cottage with textured wooden beams? The materials you choose should reflect your design intent and communicate that essence clearly.
If you’re designing a model with a focus on modern aesthetics, materials like acrylic or glass will help convey sleek, polished finishes, and transparency. For designs that aim for warmth and earthiness, materials like wood, cork, or bamboo can add a natural feel that reflects the overall atmosphere you’re going for.
Don’t forget about the scale and proportion of the model. Materials like foam board can help illustrate bulk and volume quickly, while more refined materials like basswood or metal are perfect for highlighting architectural detailing. The materials you choose will help make the design’s story clearer and more impactful, allowing the model to communicate your ideas even before anyone reads the brief.
Durability and Stability: The Test of Time
You’ve put all that effort into crafting a model—now, you want it to last. Durability is essential, especially when models will be transported, displayed, or handled by multiple people. Some materials are more durable than others. If your model needs to endure constant handling, be sure to use sturdy materials that can withstand wear and tear.
Acrylic, wood, and metal offer excellent durability and will hold up well over time. Resin and foam board, on the other hand, are better for short-term use or models that will remain stationary. If your model is being displayed outdoors or in an area with fluctuating temperatures, you’ll want to choose materials that aren’t prone to warping or damage.
It’s also important to consider environmental factors. Exposure to sunlight can fade certain materials over time, so if your model is going to be on display in a bright room or under direct light, you’ll want to opt for materials like acrylic or metal that won’t degrade or discolor. The durability of your model impacts how well it can withstand the stresses of its intended use—so choose wisely.
Factor | What to Consider | Best Materials for the Job |
---|---|---|
Project Stage | Conceptual, working, or presentation models require different levels of detail. | Conceptual: Foam board, cardboard, paper; Working: Wood, resin; Presentation: Acrylic, metal |
Budget Constraints | Stay within budget while achieving the desired quality and detail. | Affordable: Cardboard, foam; Mid-range: Wood, acrylic; High-end: Metal, resin |
Time Requirements | Speed of production impacts material choice—quicker models use lighter, simpler materials. | Quick models: Cardboard, foam; Detailed models: Acrylic, wood, resin |
Design Intent | Choose materials that reflect the aesthetic and emotional qualities of the design. | Modern: Acrylic, glass; Natural: Wood, cork, bamboo |
Durability & Stability | Ensure materials stand up to handling and environmental factors like light and temperature. | Durable: Acrylic, wood, metal; Short-term: Resin, foam |
Choosing the right materials for your architectural model is like finding the perfect puzzle pieces—it all needs to fit together just right. By considering the project stage, budget, time, design intent, and durability, you can craft a model that not only looks impressive but also communicates your ideas effectively. So whether you’re creating a quick prototype or a show-stopping presentation piece, the materials you choose will play a starring role in your model’s success.
Common Materials Used in Architectural Models
Traditional Materials: The Classics
Paper: The MVP of Conceptual Models
If you’re just getting started with a new design and need to quickly whip up a concept, paper is your best friend. Cheap, versatile, and ready for action, paper is perfect for those early design phases when you’re still testing out shapes and forms. Need to fold, curve, or make a crazy abstract design? Paper can handle it without breaking a sweat.
Advantages:
- Inexpensive: Paper’s cost-effective nature makes it a go-to for quick prototypes.
- Flexible: Bend it, fold it, tear it—paper does what you tell it to.
- Easy to Use: Just grab a pair of scissors, and you’re good to go.
Disadvantages:
- Fragile: Looks great in concept, but it doesn’t hold up well under stress.
- Not durable: Easily damaged, so don’t expect it to last through the ages.
Best Uses:
- Rapid prototyping
- Early-stage design experiments
- Testing massing and volume before committing to expensive materials
Wood (Balsa, Basswood): Lightweight, Yet Mighty
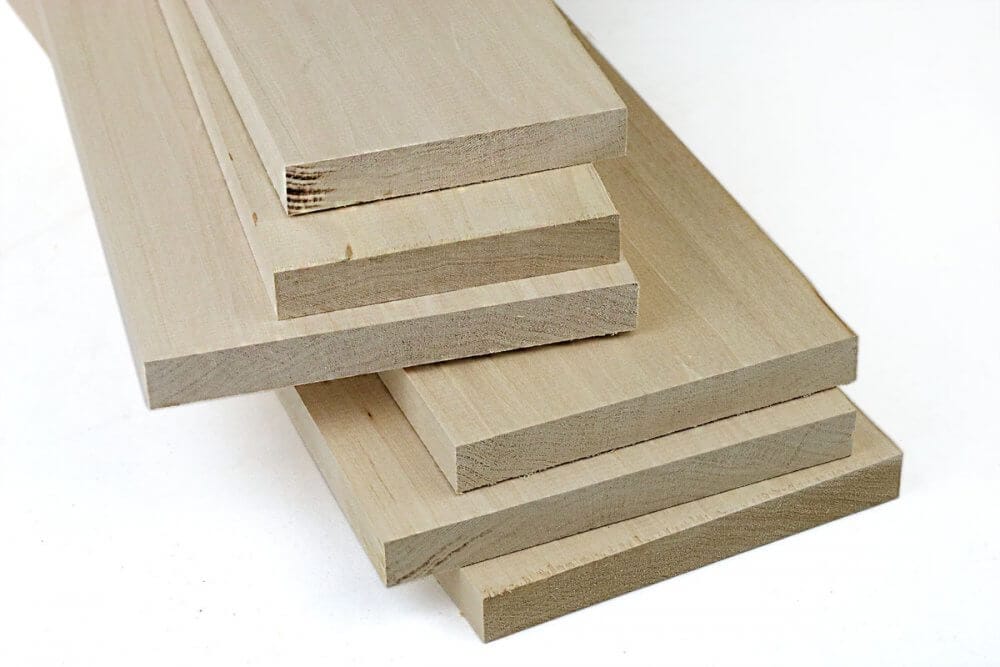
When it comes to architectural models that need both strength and detail, wood is a solid choice. Balsa and basswood are two of the most popular options for creating precise, structural elements. These woods are light, easy to cut, and can be sanded to perfection, which makes them ideal for intricate designs like doors, windows, and framing.
Advantages:
- Easy to Cut: With the right tools, you can slice through wood with ease.
- Durable: Despite being lightweight, wood holds its shape and doesn’t buckle under pressure.
- Fine Texture: Great for capturing detailed surfaces, thanks to its fine grain.
Disadvantages:
- Costly for Large Models: While it’s fantastic for small-scale work, buying large quantities of wood for a big project can add up.
- Requires Care: Can chip or splinter if not handled properly.
Best Uses:
- Detailed architectural features (windows, doors, moldings)
- Structural components in models that need extra durability
Cardboard/Chipboard: The Workhorse
Cardboard (or chipboard) might not have the glam of shiny acrylic, but it’s a tried-and-true favorite for architectural model makers on a budget. Lightweight, easy to work with, and inexpensive, cardboard is often the material of choice for initial models and massing studies.
Advantages:
- Cost-Effective: You can get a lot of mileage out of a few bucks.
- Easy to Work With: Cuts like butter and takes glue like a pro.
- Versatile: Available in various thicknesses and finishes, making it adaptable for a range of uses.
Disadvantages:
- Not Built for the Long Haul: It’s not the most durable material, so don’t expect it to last forever.
- Can Be Flimsy: If not reinforced, it can bend or warp over time.
Best Uses:
- Basic massing models
- Roadways, landscapes, and large-scale context components
- Structural parts in early-stage prototypes
Cork: The Textural Touch
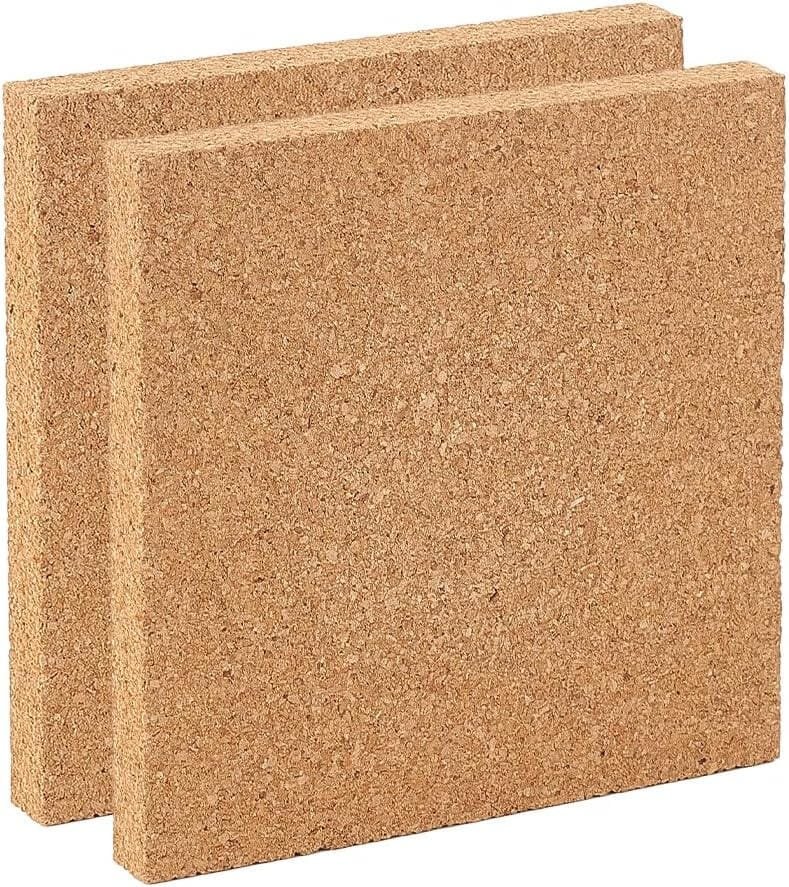
When it comes to textures, cork is the go-to material for adding that earthy, tactile quality to architectural models. It’s lightweight, easy to cut, and perfect for adding a natural aesthetic to your design. Whether you’re creating floors or base layers, cork gives your model a bit of that je ne sais quoi.
Advantages:
- Lightweight: It won’t weigh down your model, making it easier to handle and transport.
- Textured: Provides a unique surface texture that adds character.
- Easy to Cut: No need for complex tools—just scissors or a craft knife.
Disadvantages:
- Easily Damaged: Cork can stain, tear, or be crushed if mishandled.
- Delicate Finish: It’s not as polished as other materials, so it requires care in finishing.
Best Uses:
- Flooring or textural surfaces in models
- Natural finishes or landscaping details
- Base layers for additional detailing
Modern Materials: The New Kids on the Block
Foam Board: Lightweight & Ready for Anything
Foam board is a staple in architectural model-making, particularly when you need to create large-scale context models or massing studies quickly. It’s light, easy to cut, and offers clean, sharp edges that will make your model look crisp and professional. Whether you’re working on background models or a site analysis, foam board is a quick way to bring your vision to life.
Advantages:
- Quick to Work With: Cut it, glue it, and you’re done—simple as that.
- Stable and Durable: Strong enough to hold up over time, but light enough to move around.
- Clean Edges: Perfect for when you need sharp, crisp lines.
Disadvantages:
- Fragile: While it’s stable, foam can still be easily damaged if not handled with care.
- Sensitive to Environment: Temperature changes or humidity can affect foam’s integrity.
Best Uses:
- Large-scale context models
- Early-stage design exploration
- Background models for more detailed presentations
Acrylic (Plexiglass): Transparent Perfection
If you’re looking for a sleek, modern material that adds transparency and light to your model, acrylic is the way to go. This clear, plastic material is perfect for representing glass facades, windows, or other transparent architectural elements. Plus, its glossy surface reflects light beautifully, adding a touch of luxury to any model.
Advantages:
- Transparent: Perfect for showcasing glass, windows, and light interplay in models.
- Versatile: You can cut, shape, and polish acrylic to your heart’s content.
- Modern Aesthetic: The clean, glossy finish makes it ideal for contemporary designs.
Disadvantages:
- Precision Required: Cutting acrylic requires a bit of finesse, so it’s not the quickest material to work with.
- Easily Scratched: Acrylic can scratch easily, so you’ll need to handle it carefully.
Best Uses:
- Glass elements (windows, doors)
- Sleek finishes for modern designs
- Decorative elements that need to interact with light
Plastic: Affordable & Functional
Plastic is one of the most affordable and versatile materials for architectural models. Whether you’re building topographical models or landscape elements, plastic offers flexibility without breaking the bank. It’s lightweight, durable, and easy to manipulate, making it a favorite for larger-scale projects that require quick, cost-effective solutions.
Advantages:
- Lightweight: Makes handling large models a breeze.
- Affordable: Budget-friendly for larger projects.
- Versatile: Can be molded, cut, or layered to create the desired height.
Disadvantages:
- Requires Layering: To achieve certain heights, you may need to layer multiple pieces.
- Can Look Cheap: If not used carefully, plastic can appear less polished compared to more refined materials.
Best Uses:
- Topography models
- Landscape elements like hills, rivers, and roads
- Larger, simpler models that need to be cost-effective
Resin: Detail at Its Finest
For those looking to achieve intricate details, resin is the secret sauce. This material excels at replicating fine textures, creating lifelike landscapes, and even crafting figurines or water features. While resin can be more expensive and time-consuming to work with, the results are worth the effort.
Advantages:
- Precision: Great for capturing fine details and textures.
- Customizable: You can mold resin to achieve almost any texture or shape.
- Durable: Once set, resin holds up well over time.
Disadvantages:
- Expensive: Resin can be costly, especially when used for larger models.
- Time-Consuming: Working with resin requires patience and precision, making it less ideal for quick models.
Best Uses:
- Small-scale details and textures
- Water features, landscaping, and figurines
- Creating realistic models for high-end presentations
Metal (Aluminum, Copper, Steel): Strength Meets Style
When you need strength and sophistication, metal delivers. Materials like aluminum, copper, and steel are ideal for structural details, reinforcement, or representing high-end finishes. These metals add a polished, industrial feel to any model, making them perfect for designs with a modern, robust aesthetic.
Advantages:
- Durable: Metal offers strength and stability that other materials can’t match.
- Malleable: You can mold and shape metal to fit your design needs.
- High-End Finish: Perfect for showing off sleek, industrial designs.
Disadvantages:
- Requires Special Tools: Cutting and shaping metal requires specific tools and expertise.
- Can Be Expensive: Particularly if you’re working with higher-end metals.
Best Uses:
- Structural reinforcement
- Detailed high-end finishes
- Architectural elements like frames, columns, and structural beams
This comprehensive look at materials provides the variety you need for every project, from conceptual models to final presentations. The right material can elevate your design, making it more detailed, durable, and visually stunning. Whether you’re on a budget or aiming for perfection, understanding the strengths and weaknesses of each material will ensure your architectural model is ready to impress.
Eco-Friendly and Sustainable Materials for Architectural Models
Biodegradable Materials: Green is the New Black
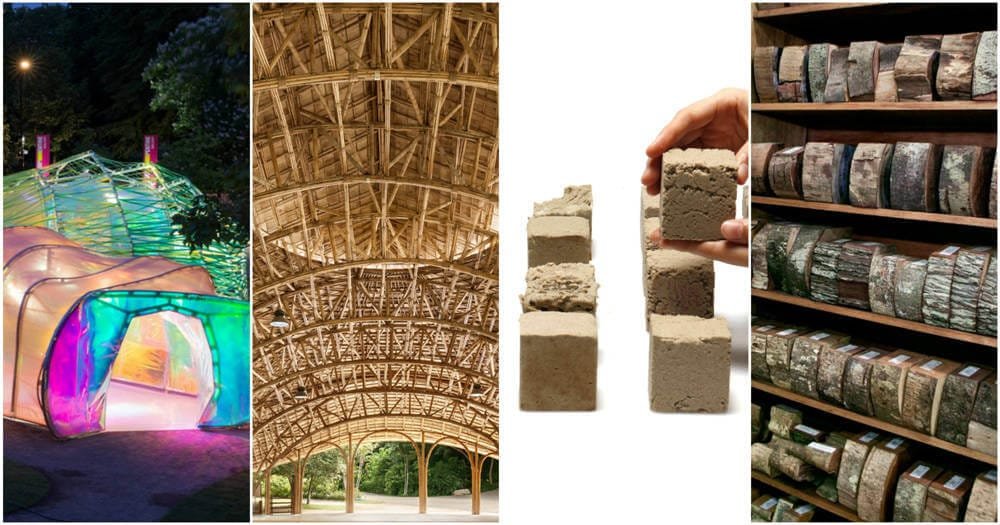
Sustainability isn’t just a buzzword—it’s the future of architecture. As the world turns greener, so too does the way we create architectural models. Enter biodegradable materials—the eco-friendly heroes that are making traditional materials look a bit… old-fashioned. These materials are not just good for the planet, they can also deliver stunning results in your models, all while reducing your environmental footprint.
Examples:
- Recycled plastics: Who knew that plastic could have a second life? Repurposing it for architectural models helps reduce waste while still delivering the durability needed for sturdy designs.
- Plant-based foams: Made from natural resources, these foams offer a more sustainable alternative to conventional foam, while still being lightweight and easy to work with.
- Biodegradable resins: A cleaner option for resin models, offering the same level of precision and detail without the long-lasting environmental impact.
Advantages:
- Eco-friendly: By using biodegradable materials, architects can significantly reduce their environmental impact and promote sustainable design practices.
- Reduces waste: These materials repurpose existing resources or are naturally recyclable, which means less junk in landfills.
- Aligns with green building practices: Perfect for projects aiming to meet eco-conscious certifications or demonstrate a commitment to sustainability.
Disadvantages:
- Durability: While biodegradable materials are great for the environment, they may not always be as durable or long-lasting as traditional materials like acrylic or metal.
- Aesthetic Precision: Some biodegradable options may lack the sleek, polished look that comes with conventional materials, so they might not always be ideal for high-end presentation models.
Best Uses:
- Projects with a sustainability focus: Whether you’re building a green skyscraper or designing a sustainable community, these materials are the perfect fit.
- Conceptual or eco-friendly models: For models meant to showcase environmentally conscious design or simply test out ideas without impacting the environment.
Recycled Materials: The Circle of Life (For Materials)
If you’re not into biodegradable materials, there’s always a solid fallback: recycled materials. These materials are the true recyclers of the architectural world, taking something old and giving it a new life—kind of like a building’s second chance at fame. Recycled paper, cardboard, and plastics aren’t just good for the environment—they’re also versatile and surprisingly effective when creating conceptual and structural models.
Examples:
- Recycled Paper/Cardboard: Perfect for conceptual models and basic presentation models, these materials offer a sustainable option for structural components without breaking the bank.
- Recycled Plastics: These sturdy materials can hold up to more demanding needs and are ideal for structural components or parts of the model that need extra strength.
Advantages:
- Sustainable: Recycled materials reduce the need for virgin resources, making them an excellent choice for eco-conscious architects.
- Reduces waste: By reusing materials that would otherwise be thrown away, you’re helping to reduce overall waste and contributing to a cleaner planet.
- Eco-conscious design: It sends a powerful message to clients, stakeholders, and the public that the project is committed to sustainability—not just in building design but in the creation process as well.
Best Uses:
- Small-scale models: Recycled materials are perfect for basic models, especially those used in conceptual exploration or testing out broad design ideas.
- Environmentally sensitive projects: When the project itself has a strong sustainability focus, using recycled materials in the models emphasizes the commitment to green design at every stage.
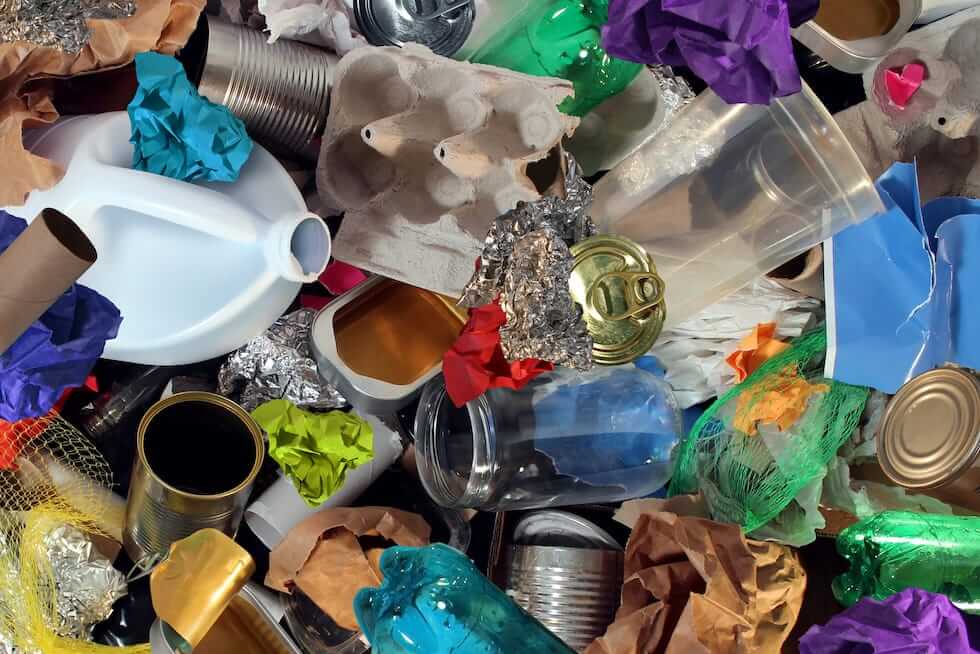
Material Type | Examples | Advantages | Best Uses |
---|---|---|---|
Biodegradable Materials | Recycled plastics, plant-based foams, biodegradable resins | Eco-friendly, reduces waste, aligns with green building practices | Projects focused on environmental sustainability |
Recycled Materials | Recycled paper/cardboard, recycled plastics | Sustainable, reduces waste, eco-conscious design | Small-scale models, environmentally sensitive projects |
By incorporating biodegradable and recycled materials into architectural models, architects and designers can help champion the cause of sustainability while still delivering effective, functional, and aesthetically pleasing models. These materials prove that making a positive environmental impact doesn’t mean compromising on quality or creativity. Whether it’s conceptual design or a high-profile sustainable project, these eco-friendly options are the way forward for any architect looking to make a mark while treading lightly on the earth.
Specialized Materials for Detailed Architectural Models
Glass: Transparency at Its Finest
If you’re aiming for precision and realism, then glass should be at the top of your materials list. This material isn’t just for windows in the real world—it’s the go-to choice for creating transparent features and glass facades in architectural models. Want to make your building look like it’s gleaming under the sun or sparkling under artificial lights? Glass is your ticket to reflecting light and showcasing transparency.
Advantages:
- Clarity: Glass offers an unparalleled level of transparency, making it ideal for representing windows, façades, and other delicate features.
- Realism: When properly incorporated, glass brings a level of realism that few other materials can match, making your models look like the real thing.
Disadvantages:
- Fragile: Glass is beautiful but easily breakable, so it needs to be handled with the utmost care. One wrong move and—whoops, there goes your perfectly crafted façade!
- Requires Precision: Cutting glass requires tools and techniques that demand careful attention, so it’s not the quickest material to work with.
Best Uses:
- Glass facades that need a touch of modern flair
- Transparent architectural features like windows and doors
- Sleek, contemporary buildings that call for that shiny, reflective finish
Synthetic Fabrics: The Fabric of Nature
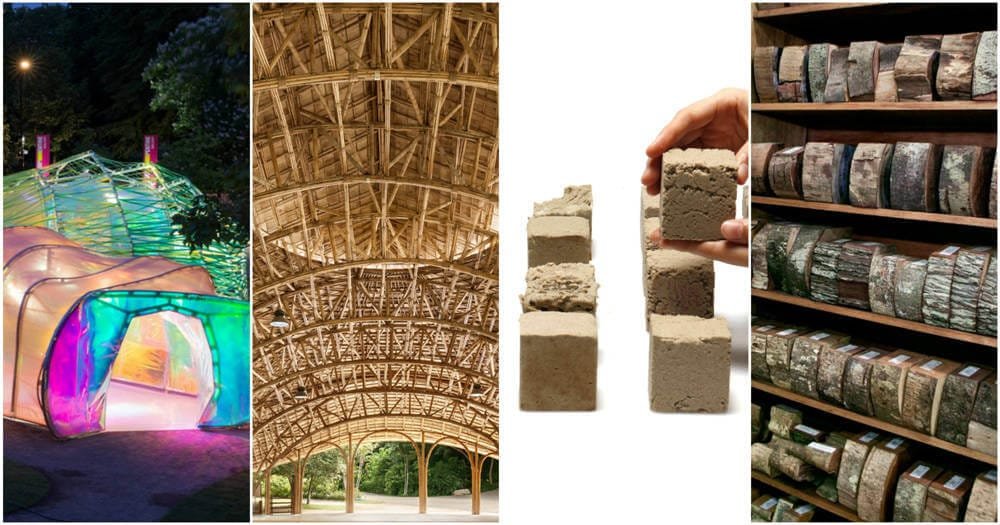
Sometimes, you need to take your model to the next level with some realistic texture. Enter synthetic fabrics, the unsung heroes when it comes to adding landscape features and terrain textures. Whether it’s for rolling hills, textured surfaces, or a shimmering body of water, synthetic fabrics help bring your model’s environment to life with a touch of flexibility and detail.
Advantages:
- Realistic Texture: Synthetic fabrics can replicate the softness of grass, the ripples of water, or the depth of mountains, making them perfect for natural landscapes.
- Flexible: These materials can be stretched, cut, and shaped, allowing you to create organic forms without the rigidity of harder materials.
Disadvantages:
- Difficult to Fit: Unlike foam or cardboard, fabrics can be tricky to glue or mold into tight spaces without losing their natural flow.
- Trickier to Handle: It requires patience to get the fabric into the right shape or texture, and they don’t always stick like you’d want them to.
Best Uses:
- Landscape features: Create lush, rolling fields or natural terrains with fabric that mimics the organic look of grass or dirt.
- Water Bodies: Synthetic fabrics can simulate the movement and texture of water with stunning effect.
- Textured surfaces: Perfect for realistic finishes like fields, forests, or gravel roads in your architectural landscape.
Photoluminescent Materials: Glow in the Dark? Yes, Please.
Ever wanted your model to shine—literally? That’s where photoluminescent materials come into play. These materials absorb light and then release it in the form of a soft glow once the lights go out. They’re perfect for creating dramatic lighting effects or highlighting specific features of your model, like emergency exit routes or lighting systems.
Advantages:
- Dramatic Effect: Imagine your model coming alive in the dark with glowing elements! This effect can highlight critical features, making your model not just a static representation but an interactive experience.
- Unique Visuals: They create eye-catching effects that will make your model stand out and dazzle your audience. Perfect for showing off lighting design or innovative features.
Disadvantages:
- Not for Every Model: While photoluminescent materials can create stunning effects, they aren’t always practical for all projects, especially if they aren’t central to the design.
- Costly: These materials tend to be on the pricier side, so they may not fit within every project’s budget.
Best Uses:
- Lighting Systems: Highlight innovative lighting or emergency exit paths with these glowing materials.
- Unique Visual Effects: Use them to create that “wow” factor, whether for artistic effect or to showcase specific features like nighttime illumination.
- Interactive models: Make your model come alive by incorporating photoluminescent elements that show how the building or space behaves under different lighting conditions.
Material Type | Examples | Advantages | Best Uses |
---|---|---|---|
Glass | Transparent elements, glass facades | Clarity, realism, reflective properties | Windows, facades, modern architectural features |
Synthetic Fabrics | Landscape fabrics, water bodies, textured surfaces | Realistic textures, flexibility | Terrain modeling, landscape features, water features |
Photoluminescent Materials | Glow-in-the-dark materials | Dramatic effects, unique lighting, interactive | Lighting systems, emergency exits, nighttime visuals |
Incorporating specialized materials like glass, synthetic fabrics, and photoluminescent elements into your architectural models adds depth, realism, and visual intrigue. Whether you’re aiming for modern elegance with sleek glass facades or a dramatic glow that brings your model to life, these materials elevate your designs and help tell a more dynamic story. With the right tools and a bit of creativity, your models won’t just be accurate—they’ll be extraordinary.
Choosing the Right Material for Your Architectural Model
Design Type: Tailoring Your Material to the Model’s Purpose
Selecting the perfect material for your architectural model isn’t just about choosing what looks good—it’s about matching the material to the purpose of the model. Think of it like picking the right pair of shoes for an event: You wouldn’t wear flip-flops to a black-tie dinner, and you wouldn’t wear dress shoes to a hike (unless you’re some kind of fashion-forward adventurer). The same applies to architectural models.
For conceptual testing, speed and flexibility are key. You need materials that allow you to quickly explore ideas, test shapes, and iterate. Paper, cardboard, and foam board are your best bets here. They’re lightweight, easy to cut, and cheap enough that you don’t feel guilty about throwing away a few versions before landing on the right one.
When it’s time to get serious, and the model is heading toward presentation or client engagement, your material choices need to be more refined. For high-detail models that will be used to impress investors or stakeholders, materials like wood, acrylic, and resin are ideal. These materials not only look more polished, but they also provide a cleaner finish and structural integrity. Clients expect sophistication and precision at this stage—so the material should reflect that.
Practical Considerations: The Logistics of Material Selection
We all love a good design challenge, but let’s be real—practicality plays a big role in material selection. Durability, cost, ease of use, and availability should be your guiding stars. After all, there’s no point in choosing the fanciest material if it’s too expensive or difficult to work with.
- Durability: How well does the material hold up? Will it stand the test of time, or is it fragile and prone to damage? For long-term projects, wood, acrylic, and metal are strong contenders. For quick prototypes or conceptual models, materials like cardboard and foam might work fine, but they won’t last forever.
- Cost: Budget plays a major role. If you’re working with limited resources, go for cost-effective materials that don’t sacrifice quality. Cardboard, foam board, and recycled materials can give you a lot of bang for your buck.
- Ease of Use: Some materials are a breeze to work with, while others require special tools and skills. Foam board? Easy. Acrylic or metal? Not so much unless you have a laser cutter and some experience in precision cutting.
- Availability: Make sure you can easily get your hands on the materials you need. If you’re in a rush, a trip to the local hardware store or art supply shop for cardboard and foam board is a lot easier than sourcing specialty resin or metal.
Skill and Tools: Complexity Adds Another Layer
It’s no secret that some materials are more complex to work with than others. Just like some recipes require a sous-vide machine and a sprinkle of gourmet salt, others are fine with instant noodles. If you’re working with a simple design and you’ve got a tight deadline, the complexity of the material won’t matter much. But if you’re diving into something more intricate, be prepared to bring out the big guns—or at least the proper tools.
Some materials require specific tools, and if you don’t have access to them, you could end up frustrated (and possibly with a few misplaced cuts). Acrylic and wood can be a dream to work with if you have access to laser cutters or precision saws, but without these tools, they can quickly become a nightmare. Materials like foam or cardboard? They’re forgiving and easy to manipulate with basic craft knives and scissors—no special tools required.
The more complex the material, the more time and skill you’ll need. So, be honest with yourself: Are you ready for the challenge? Do you have the necessary tools? If you’re unsure, it might be better to go with something simpler and more forgiving.
Client Preferences: Green or Clean?
Not every client is focused solely on aesthetics. Some may have a specific philosophy they want to align with, and materials can play a big role here. For eco-conscious clients, sustainable and recycled materials are a priority. For others, they might be after a particular look—say, a sleek modern finish or a rustic, natural feel.
- Eco-Friendly Materials: If sustainability is a priority, think about incorporating biodegradable materials, recycled paper, wood, or even plant-based foams. These are perfect for clients who want their design to align with green building practices and environmental stewardship.
- Aesthetic Preferences: Some clients may have a preference for a specific material aesthetic—whether they’re into high-end finishes like acrylic and metal, or they want something that feels earthy and authentic like wood or cork. Understanding their style will help steer your material choices.
Consideration | What to Keep in Mind | Ideal Materials |
---|---|---|
Design Type | Choose materials that fit the stage—conceptual, working, or presentation. | Conceptual: Foam board, cardboard; Presentation: Wood, acrylic, resin |
Practical Considerations | Durability, cost, ease of use, and availability all matter in the material choice. | Budget-Friendly: Cardboard, foam; Durable: Wood, acrylic, metal |
Skill and Tools | Materials require different tools and skills—be honest about your ability. | Easy to Use: Foam board, cardboard; Complex: Acrylic, wood, metal |
Client Preferences | Consider eco-conscious designs or specific material preferences. | Eco-Friendly: Recycled materials, biodegradable options; Aesthetic: Acrylic, wood |
Choosing the right material for your architectural model isn’t a decision to take lightly. It’s about finding the perfect balance between your design goals, budget, and available tools. With a little thought, you’ll have the perfect material for your project—whether it’s a quick conceptual model or a show-stopping presentation piece that wows your clients. So, pick wisely, and remember, the material you choose is just as important as the design itself!
Tips for Working with Architectural Model Materials
Material Handling: Crafting Your Model with Precision
When it comes to architectural model-making, handling materials properly is half the battle. Whether you’re cutting, gluing, or finishing, each material comes with its own quirks, and mastering those is what separates the amateurs from the pros. Think of it like baking a cake—you can’t just throw the ingredients together and hope for the best. You need the right techniques, tools, and a little bit of finesse.
Cutting Materials:
When it comes to cutting, precision is key. You don’t want to end up with jagged edges on a clean-cut design. For paper, cardboard, and foam board, a sharp utility knife is your best friend. If you’re working with thicker materials like wood, you’ll want something stronger—handsaws, jigsaws, or even a laser cutter for ultra-fine cuts. Always measure twice, cut once! And don’t forget about safety—be sure to use a stable cutting surface (like a cutting mat) to protect both your materials and your work surface.
Bonding Materials:
When it comes to bonding materials together, the right adhesive can make or break your model. Wood glue works wonders for wood and balsa projects, while foam-safe glue is your go-to for anything foam-based. Be cautious with superglue—it’s quick and strong, but if you’re not careful, it can make a mess. Acrylic cement is a must for acrylic—this glue melts the edges slightly, forming a strong bond that looks like it’s almost seamless.
Finishing Your Model:
After all that cutting and gluing, you’ll need to make sure your model has a clean, polished finish. For wood, sanding is key to smooth out rough edges. Acrylic can be polished with a soft cloth or special polishing compound for that shiny, professional look. Remember: a little goes a long way, so be careful not to overdo it—otherwise, you’ll find yourself sanding away all your hard work.
Tools and Equipment: The Right Tools for the Job
When it comes to architectural models, tools and equipment can be the difference between a frustrating day of mistakes and a smooth, successful project. You don’t need a workshop full of gadgets to get the job done, but having the right tools will make your life a whole lot easier.
Laser Cutters for Acrylic:
Laser cutters are the rock stars of the architectural model-making world. They allow you to cut acrylic, wood, plastic, and even thin metal with precision. These machines use a laser to make perfect, smooth cuts, reducing the chance of imperfections. If you’re working on a detailed presentation model, a laser cutter will help you create fine, sharp details with ease.
Foam Cutters for Foam Board:
For quick, clean cuts in foam board or polystyrene, a foam cutter is your go-to tool. These tools use a heated wire to slice through foam like a hot knife through butter. It’s fast, clean, and it won’t leave you with a pile of tiny foam crumbs. Just be sure to work in a well-ventilated area—burnt foam isn’t exactly a pleasant smell.
Craft Knives for Paper and Cardboard:
For paper, cardboard, and chipboard, a craft knife is your best friend. It’s cheap, reliable, and easy to control for intricate cuts. Make sure to use a fresh blade to avoid any dull, ragged edges—after all, your model’s finish is only as good as the tools you use.
Rulers, Templates, and Scalpels:
Whether you’re cutting or measuring, accuracy is key. A good metal ruler will ensure your cuts are straight, while templates help you get consistent shapes every time. For detailed cuts or intricate designs, a scalpel offers greater precision than a regular craft knife.
Common Mistakes to Avoid: Learn From the Pros (and the Fails)
Even seasoned professionals can slip up during model-making. But with a little know-how, you can avoid the rookie mistakes that turn a good model into a disaster. Here are some common pitfalls to watch out for:
Uneven Cuts:
If your cuts are uneven, the whole model can start to look sloppy. Whether you’re cutting wood, foam, or acrylic, measure twice, cut once. And don’t rush it—accuracy matters more than speed. A good, clean cut means your pieces will fit together perfectly, saving you time and frustration in the long run.
Using the Wrong Glue:
Not all adhesives are created equal. Using the wrong glue can cause unsightly marks, weak bonds, or sticky messes. For example, using PVA glue on acrylic can result in cloudy, uneven seams. Acrylic cement or foam-safe glue will do the trick. Make sure you read the label, and always test the glue on a scrap piece before committing to the whole model.
Miscalculating Material Quantities:
One of the most frustrating things in model-making is running out of materials halfway through. You don’t want to be in the middle of creating your masterpiece, only to realize you’re short by a few sheets of foam or an acrylic panel. To avoid this, plan ahead—take measurements and factor in some extra material to account for mistakes, test pieces, or changes in design.
Not Accounting for Material Shrinkage:
Certain materials like foam or plastic may shrink or expand depending on the environment. If you’re gluing a piece and it has the potential to shrink, you’ll end up with gaps or misalignment once it’s set. Always take these factors into account when measuring and assembling your model.
Mistake | What to Avoid | How to Fix It |
---|---|---|
Uneven Cuts | Rushing through cuts or using the wrong tools. | Use a sharp craft knife, measure twice, and cut slowly. |
Wrong Glue | Using the wrong adhesive for materials. | Choose adhesives based on material type (e.g., acrylic cement for acrylic). |
Miscalculating Quantities | Running out of materials mid-project. | Plan ahead, measure twice, and buy extra materials. |
Material Shrinkage | Ignoring shrinkage or expansion in certain materials. | Account for material behavior when designing and assembling. |
By following these tips, you’ll be well on your way to creating architectural models that are precise, professional, and durable. Master the art of handling materials, using the right tools, and avoiding common mistakes, and your models will stand out for all the right reasons. With the right preparation, you’ll turn that humble lump of foam or acrylic into a modeling masterpiece that shines in design and execution.
Conclusion: Selecting the Perfect Materials for Your Architectural Models
Recap: The Right Material for the Right Stage
Choosing the perfect material for your architectural model is like choosing the right shoes for a marathon—you wouldn’t wear flip-flops for a 26-mile run, right? The material you pick needs to match the stage of your project, as well as the level of detail, durability, and aesthetic appeal required.
For early conceptual models, think light, cheap, and flexible. Paper, foam board, and cardboard let you quickly explore massing, shape, and form without getting bogged down by detail. But as your design matures, so should your material choices. Wood, acrylic, and resin are perfect for the working models and presentation pieces that need to showcase your design’s refinement, adding the polish and precision that clients and stakeholders love to see.
Selecting materials is not just about what looks good on paper (pun intended), but about making sure they serve the project’s purpose and bring your ideas to life in the most effective way possible. It’s not always about picking the most expensive or fancy material; it’s about choosing the right material for the job at hand.
Final Thoughts: Experiment, Play, and Build Better Models
The beauty of architectural model-making is that it’s as much about experimentation as it is about precision. Don’t be afraid to play around with materials, mix and match, and see how different substances interact with your design ideas. Whether you’re a seasoned pro or just starting out, exploring new materials can elevate your models from “good” to “wow.”
Some of the best ideas come from the unexpected—maybe biodegradable foams or recycled plastics could bring a fresh, sustainable touch to your next project. The world of model-making materials is vast and full of untapped potential. So, why not dive into something new? Experimentation will help you find the right fit for your specific needs and will likely spark even more creativity in the process.
Call to Action: Elevate Your Design with Professional Help or New Materials
Ready to take your models to the next level? If you’re feeling adventurous (or just need an expert hand), there’s always the option to explore professional model-making services. These services bring years of experience and high-end tools to the table, ensuring your model is nothing short of perfect.
Or, if you’re feeling a bit more DIY, experiment with new materials. Biodegradable resins, 3D printed elements, or even unconventional options like photoluminescent materials could be exactly what you need to push the boundaries of what’s possible in architectural model-making. Get your hands dirty, get creative, and take your design expression to new heights!
Choosing the right material isn’t a one-size-fits-all approach—it’s about matching the material to the project’s stage, purpose, and aesthetic needs. So whether you’re playing with conceptual designs or fine-tuning a presentation model, the right material can make all the difference. Experiment, explore, and let your materials help you bring your architectural vision to life.
FAQ: Everything You Need to Know About Materials for Architectural Models
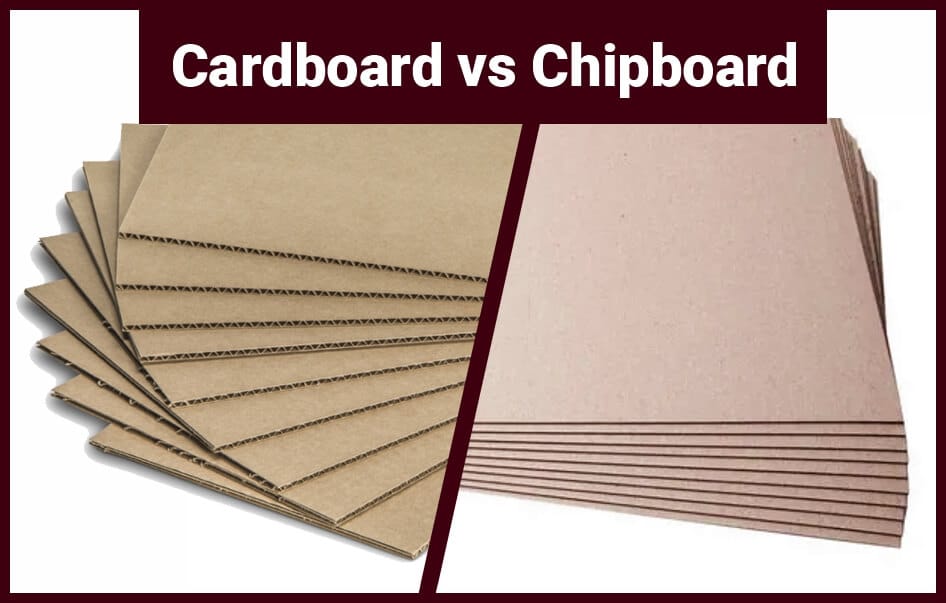
What Are the Best Materials for Architectural Models?
The best materials for architectural models depend on the purpose of the model and the stage of the design process. For conceptual models, materials like foam board, cardboard, and paper are perfect because they’re cost-effective, easy to manipulate, and quick to work with. As you move into more detailed or presentation models, you’ll want to upgrade to materials like acrylic, wood, and resin, which offer more refinement, durability, and precision. If your model is all about realism and modern finishes, metal and glass should definitely be on your list.
For eco-conscious projects, biodegradable materials, recycled plastics, and plant-based foams are becoming increasingly popular. These materials not only reduce environmental impact but also add a unique touch to your models, demonstrating your commitment to sustainability.
How Do I Choose Materials for Architectural Models?
Choosing the right material for your architectural model is like picking the right tool for the job—every material has its purpose, and knowing what you need is half the battle. Here are the key factors to consider:
- Project Stage: If you’re in the early conceptual phase, go for flexible, cheap materials like cardboard and foam. When the design matures, high-detail materials like acrylic and wood will be more appropriate.
- Budget: Material costs vary greatly, so consider your budget constraints. You don’t want to break the bank on a model that’s just for internal testing.
- Time Constraints: If you’re on a tight schedule, go with materials that are quick and easy to work with, like foam board or cardboard. For more complex models, materials like acrylic or wood require more time and effort.
- Design Intent: Think about what your model needs to convey. If you want to showcase modern or sleek aesthetics, acrylic and metal are your go-to materials. For rustic or natural designs, wood and cork will work wonders.
What Materials Are Used in Architectural Models for Presentation?
When you need a model that impresses clients, stakeholders, or investors, the material choice becomes crucial. Presentation models demand high precision, clean finishes, and the ability to highlight key design features.
- Acrylic: Ideal for transparent elements like windows and facades, acrylic offers a sleek, polished look that gives your model a modern feel.
- Wood: Basswood and balsa wood are lightweight yet durable, perfect for creating intricate details such as framing, doors, and windows.
- Resin: For adding small-scale detailing like figurines, landscaping, or even water features, resin allows for high accuracy and customization.
- Metal: For models that need extra strength or to reflect a more industrial look, metals like aluminum or steel are perfect for structural elements and high-end finishes.
- Foam Board: For large, basic context models or massing studies, foam board is cost-effective and easy to work with.
The material you choose should elevate your design, making it stand out and speak volumes to those viewing it.
What Eco-Friendly Materials Can Be Used for Architectural Models?
Sustainability is no longer just a trend—it’s a necessity. Fortunately, there’s a growing range of eco-friendly materials that are perfect for architectural model-making. These materials not only reduce your carbon footprint but can also lend a unique aesthetic to your design.
- Biodegradable Materials: Options like plant-based foams and biodegradable resins provide sustainable alternatives to traditional plastics, and they still deliver the detail and precision needed for high-quality models.
- Recycled Plastics: By using recycled plastics, you’re giving old materials a second life, while also maintaining the durability and strength required for structural elements in your models.
- Recycled Paper/Cardboard: These materials are widely available, cost-effective, and perfect for conceptual or small-scale models. By choosing recycled paper or cardboard, you can stay true to sustainable principles without compromising on model quality.
- Recycled Wood: For those looking to add a natural touch while staying eco-conscious, recycled wood is a great option. It provides the same warmth and texture as new wood, but without the environmental impact of cutting down trees.
Choosing these eco-friendly materials helps bring your sustainability goals into focus while still producing detailed, high-quality models.
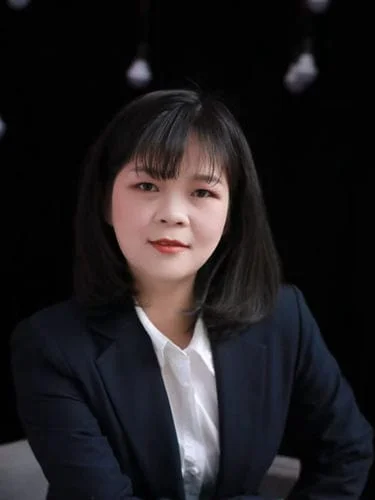