Ever tried explaining a complex factory layout or a sophisticated piece of machinery using just words or flat drawings? It’s tough. That’s where industrial models come in. These aren’t just toys; they are meticulously crafted, scaled physical replicas of industrial facilities, equipment, or processes.
From intricate power plants to streamlined production lines, these tangible representations serve as powerful tools. They bridge the gap between abstract concepts and physical reality, aiding in everything from crucial design decisions and stakeholder communication to compelling sales presentations and effective training. This guide will delve deep into the world of industrial models, exploring their creation, applications, and enduring value in today’s technical landscape.
Table of Contents
Introduction: Why Industrial Models are Indispensable in the Modern Age
Imagine trying to convey the intricate dance of a complex manufacturing process or the sheer scale of a new power plant using only words and flat blueprints. It’s a challenge, right? This is where the industrial model steps in. Far more than just a miniature replica, it’s a powerful communication and planning tool that brings complex industrial concepts vividly to life in three dimensions.
These physical representations bridge the critical gap between abstract ideas and tangible reality, offering clarity where words or 2D drawings might fall short. Think of them as storytellers, educators, and problem-solvers, all rolled into one meticulously crafted object.
Defining the Industrial Model: More Than Just Miniature Replicas
An industrial model is a physical, often scaled, representation of factories, machinery, facilities, or entire industrial processes. But its role is far more versatile than you might initially assume:
- As a Creative Tool: They serve to express manufacturing processes or replicate engineering facilities. Sometimes the goal is to demonstrate a principle, other times it’s about capturing every minute detail with high fidelity.
- As a Sales & Marketing Instrument: Models tell compelling stories. They showcase unique features in an easily understandable way, generating excitement and engaging potential clients or investors much more effectively than a slideshow ever could.
- As an Engineering & Design Tool: Crucially, they allow for the visualization, testing, and planning of layouts, ergonomics, and functionality long before committing to expensive construction or production.
- As a Communication Bridge: Models create a common ground for understanding among diverse stakeholders – from engineers and architects to investors, management teams, and even the public. They speak a universal language.
The Growing Importance in Manufacturing, Engineering, and Beyond
In an increasingly complex and technology-driven world, clear communication and precise planning are paramount for success. Industrial models provide exactly that: a tangible way to share ideas, validate designs, and avoid costly mistakes. Whether optimizing factory layouts, securing funding for a major infrastructure project, or presenting groundbreaking technology at trade shows, their significance is undeniable and continues to grow. They are no longer just nice-to-haves; in many complex projects, they are essential.
Brief Overview of This Guide (Scope)
This comprehensive guide dives deep into the multifaceted world of industrial models. We will explore precisely what they are, uncover why they are so critically important, detail the step-by-step process of their creation, examine the technologies involved, and offer guidance on selecting the right model maker for your specific project. Whether you are an engineer seeking planning clarity, a designer visualizing a concept, a marketing professional aiming to captivate an audience, or an investor evaluating potential, you will find valuable insights here. Let’s embark on this journey from blueprint to tangible reality.
What Exactly Constitutes an Industrial Model? Unpacking the Concept
While the term “industrial model” sounds specific, it actually encompasses a fascinating range of physical representations. Understanding these variations is key to appreciating their versatility and choosing the right type for a given purpose.
Defining the Scope: From Simple Concepts to High-Detail Replicas
The complexity and level of detail in an industrial model vary significantly based on its intended function:
- Conceptual Models: Often created early in the design process, these models might be simpler, focusing on demonstrating a basic working principle, overall form, or spatial layout. They are excellent for brainstorming and initial feasibility checks. Think of them as 3D sketches.
- Presentation Architectural Models: Here, visual appeal and high detail are paramount. These models showcase buildings, facilities, or entire industrial sites with remarkable accuracy and aesthetic quality. They are frequently used for client presentations, public exhibitions, or securing regulatory approvals.
- Functional Prototypes: Going beyond static representation, these models incorporate moving parts or simulate specific functions to test mechanical operations, ergonomic handling, or process flows. They are invaluable for validating design choices before committing to tooling or production.
- Scale Models: The primary focus here is the precise, proportional reduction (or sometimes enlargement) of the original object. Maintaining scale accuracy is crucial for understanding size relationships, planning layouts, and ensuring spatial integrity.
The Core Purpose: Making the Intangible Tangible
Regardless of their specific type, all industrial models share a fundamental purpose: to translate abstract plans and complex ideas into a physical, experienceable form.
- From 2D to 3D: They transform flat blueprints, technical drawings, and CAD files into three-dimensional objects, providing an intuitive understanding of space and form that 2D representations often lack. You can walk around it, view it from different angles – something impossible with a drawing.
- Visualizing Complex Systems and Workflows: Intricate piping networks, multi-stage production lines, or complex facility layouts become instantly clearer when represented physically. Bottlenecks, potential clashes, or inefficiencies are often spotted immediately.
- Representing Scale: Models master the challenge of scale. Massive refineries or power plants can be brought down to a manageable tabletop size for review, while tiny, intricate components like micro-valves can be scaled *up* to reveal their details.
“An industrial model tells the entire story. Whether you are communicating… with the builder, investors, customers, or city commissioners, an industrial model accurately portrays the idea and vision.”
Distinguishing Industrial Models from Other Model Types
While overlaps exist, industrial models typically differ from purely architectural models by placing a greater emphasis on processes, functionality, technical equipment, and operational flows within a facility. Unlike scientific models, which often illustrate theoretical concepts or natural phenomena, industrial models almost always represent specific, tangible industrial objects, systems, or planned projects.
The Crucial Role and Importance of Industrial Models Across Industries
Investing in an industrial model isn’t just about creating a fancy miniature; it’s a strategic decision with far-reaching benefits that impact efficiency, communication, safety, and the bottom line. Let’s explore why they are considered so essential in today’s industrial landscape.
Why Invest in Industrial Models? Core Benefits Overview
The advantages of using physical models are numerous and compelling. Here’s a quick summary of the key benefits (which we will explore in more detail later):
Benefit Category | Key Advantage |
---|---|
Design & Planning | Enhanced Visualization & Understanding |
Effective Design Testing & Validation | |
Increased Safety in Design & Training | |
Communication & Collaboration | Improved Stakeholder Communication |
Facilitating Fundraising & Approvals | |
Efficiency & Cost | Significant Cost & Time Savings |
Sales & Marketing | Powerful Marketing & Sales Impact |
The Impact on Modern Manufacturing Processes
In the competitive world of modern manufacturing, optimizing every aspect of production is key. Industrial models play a vital role in achieving this efficiency:
- Optimizing Production Flow and Efficiency: By creating a physical representation of the factory floor, teams can simulate the movement of materials, parts, and personnel. This helps identify bottlenecks, reduce travel distances, and streamline the entire workflow before a single machine is installed.
- Streamlining Factory Layouts: Models allow planners to experiment with different arrangements of machinery, workstations, storage areas, and buffer zones. Finding the optimal layout maximizes space utilization and minimizes potential conflicts.
- Ensuring Correct Positioning of Integrated Elements: From conveyor systems and robotic arms to safety barriers and utility lines, models ensure that all components are placed correctly relative to each other, avoiding costly clashes or accessibility issues during installation and operation.
As one source puts it, architectural models (in the industrial context) ensure “not only productivity and a high-performance infrastructure are ensured, but also a correct positioning of all integrated elements.”
Necessity in Large-Scale and Complex Projects
The larger and more intricate a project, the more indispensable an industrial model becomes. Its ability to provide a holistic, easily understandable overview is unmatched, particularly in:
- Civil Engineering Projects: Visualizing massive structures like bridges, complex freeway interchanges, airport expansions, or rail projects requires a scaled representation to grasp the overall scope and interactions.
- Energy Sector: Planning vast facilities like nuclear power plants, sprawling refineries, offshore oil rigs, or large-scale renewable energy farms (wind/solar) relies heavily on models for site planning, equipment placement, and stakeholder communication.
- Complex Manufacturing Facilities: Intricate processes in automotive plants, pharmaceutical production, or chemical processing often involve interconnected systems that are best understood and optimized using a physical model.
The Step-by-Step Process of Bringing an Industrial Model to Life
Creating a high-quality industrial model is a meticulous process that blends artistic skill, engineering precision, and technological prowess. It typically unfolds in several distinct phases, each crucial for achieving the desired outcome.
Phase 1: Conceptualization and Design Foundation
Every great model starts with a clear idea and a solid plan.
- Understanding Purpose and Requirements: What is the model’s primary goal? Who is the intended audience? What level of detail and accuracy is needed? Is interactivity required? Clarifying these points upfront is essential.
- Brainstorming and Initial Sketching: Ideas are explored, concepts are visualized through rough sketches, and the basic form and key features are outlined.
- Collaborative Design Team Efforts: Designers, engineers, model makers, and often the client work together to refine the concept, ensuring everyone is aligned on the vision.
The Critical Role of Blueprints
The blueprint (or technical drawing/CAD file) serves as the definitive guide for the model maker. It’s the source of truth for dimensions, layout, and details.
- Understanding Key Elements: Model makers must accurately interpret dimensions, scale indicators, equipment placements, material specifications, and assembly instructions.
- Interpreting Layouts and Diagrams: Factory plans, process flow diagrams (PFDs), piping and instrumentation diagrams (P&IDs), and equipment schematics must be thoroughly understood to translate them into three dimensions.
- Foundation for Accuracy: Any misinterpretation of the blueprint can lead to inaccuracies in the model, potentially propagating errors into the real-world project. Careful study and verification are paramount. “Blueprints lay the foundation for accuracy.”
Phase 2: Digital Design – Precision with CAD Modeling
Once the concept and blueprints are clear, the design moves into the digital realm.
- Creating Precise Digital Models: Using specialized Computer-Aided Design (CAD) software, designers create a highly accurate, detailed 3D virtual representation of the object or facility. Software like AutoCAD, SolidWorks, Rhino, or Revit might be used depending on the application.
- Detailed Visualizations and Simulations: CAD allows for realistic rendering, virtual walkthroughs, and even simulations of movement, clearance checks, or simple process flows, aiding in early design validation.
- Providing Exact Manufacturing Data: The digital CAD model provides the precise geometric data (measurements, coordinates, specifications) needed to drive automated manufacturing processes like CNC machining and 3D printing.
Phase 3: Material Selection – Choosing the Right Medium
Selecting the appropriate materials is crucial for the model’s appearance, durability, detail level, and cost. The choice depends on multiple factors:
Material | Key Characteristics | Common Applications in Industrial Models |
---|---|---|
Foam / Foam Board (e.g., Polystyrene, Polyurethane) | Lightweight, easy to cut/shape, cost-effective, good for volume studies. | Initial massing/conceptual models, terrain representation, base structures, large simple forms. |
Plastics (e.g., ABS, Acrylic/PMMA, PVC, Styrene) | Versatile, good detail possible, durable, paintable, some are transparent (Acrylic). | Structural components, housings, pipes, tanks, windows, detailed parts, often used in 3D printing (ABS, PLA). |
Wood (e.g., Basswood, Balsa, Plywood) | Good balance of strength and workability, natural aesthetic, stable for bases. | Baseboards, larger structural frameworks, architectural elements, landscape contouring. |
Metals (e.g., Aluminum, Brass, Steel) | High strength, precision possible (machining), realistic appearance for metal parts, durability. | Functional prototypes, high-detail machinery components, structural supports, realistic piping. |
Resins (e.g., Epoxy, Polyurethane, Photopolymers for 3D printing) | Excellent for fine details (especially 3D printing – SLA/DLP), castable, can be clear or opaque. | Highly detailed small parts, intricate machinery, figures, casting masters. |
Composites / Other | Fiberglass, carbon fiber (strength/lightweight), plaster, specialized modeling clays, landscaping materials (flock, turf). | Large durable structures, custom shapes, terrain modeling, realistic ground cover. |
Phase 4: Fabrication and Construction – Building the Model
This is where the digital design translates into physical components using various techniques:
Fabrication Technique | Description | Primary Advantages |
---|---|---|
3D Printing (Additive Manufacturing) | Building parts layer-by-layer from digital data using materials like plastic filament (FDM), liquid resin (SLA/DLP), or powder (SLS/MJF). | High precision for complex geometries, speed for prototypes (“Rapid Prototyping”), ability to create intricate internal features. |
CNC Machining (Subtractive Manufacturing) | Computer-controlled cutting tools (mills, lathes) remove material from a solid block (metal, plastic, wood) to achieve the desired shape. | Very high accuracy and surface finish, excellent for strong, functional parts from robust materials. |
Laser Cutting | Using a focused laser beam to cut precise shapes from flat sheet materials (acrylic, wood, card, thin plastic). | Fast, clean cuts, excellent for layered constructions, façade details, or template creation. |
Handcrafting | Skilled artisans shape, join, sand, and finish components using traditional tools (knives, files, saws, sculpting tools). | Allows for unique customization, artistic interpretation, fine-tuning details, complex assemblies, finishing touches. |
Thermoforming / Vacuum Forming | Heating a plastic sheet until pliable, then draping or sucking it over/into a mold. | Efficient for producing multiple copies of thin-walled shells or simple curved shapes. |
Casting | Pouring liquid material (resin, plaster, sometimes metal) into a mold to replicate a shape. | Good for producing multiple identical parts, especially those with complex surfaces. |
Essential Tools for Precision Craftsmanship
Beyond the high-tech machinery, a model maker’s bench relies on essential hand tools for precision work:
- Precision craft knives (X-Acto style), scalpels, and self-healing cutting mats.
- Steel rulers, calipers, squares, and other measuring instruments.
- A variety of files, sanding blocks, and abrasive papers/sticks for shaping and smoothing.
- Tweezers, clamps, vices, and jigs for holding small parts during assembly and gluing.
- Specialized adhesives suitable for bonding different materials (plastics, wood, metal).
- Airbrushes and fine paintbrushes for applying paint and finishes.
Phase 5: Assembly and Finishing – Adding Realism and Detail
Once the individual components are fabricated, they must be carefully assembled to create the final model.
- Precise Fitting: Ensuring all parts align correctly, gaps are minimized, and the overall structure is accurate according to the design. This requires patience and skill.
- Ensuring Functional Integrity: If the model includes moving parts, careful assembly is needed to ensure they operate smoothly without binding.
Finishing Techniques: The Art of Realism
The finishing stage transforms a collection of parts into a convincing representation of reality. This involves:
- Surface Preparation: Filling minor imperfections, sanding surfaces smooth for painting, masking areas not to be painted.
- Priming and Painting: Applying primer for better paint adhesion, followed by accurate color coats, often using airbrushing for smooth gradients and fine details. Weathering effects (rust, dirt, wear) can add realism.
- Applying Decals and Markings: Adding logos, safety labels, instrument panels, signage, and other markings for authenticity.
- Texturing: Creating realistic surface textures – the roughness of concrete, the grain of wood, the sheen of polished metal, or the matte finish of certain plastics.
- Adding Entourage: Incorporating scale elements like miniature people, vehicles, trees, shrubs, grass, water effects, etc., to give context, scale, and life to the model.
Phase 6: Integration of Interactive Elements (Where Applicable)
Many modern industrial models go beyond static displays to actively engage the viewer:
- Lighting Systems: Strategically placed LEDs can illuminate buildings, highlight specific process flows or critical paths, indicate operational status, simulate nighttime conditions, or simply enhance visual appeal.
- Moving Parts: Incorporating motors and mechanisms to animate conveyor belts, rotating turbines, robotic arms, or other machinery provides a dynamic demonstration of operations.
- Simulated Effects: Using small smoke generators, water pumps, or specialized lighting can realistically simulate steam, fluid flow, sparks, or other industrial phenomena.
- Sound Effects: Adding appropriate sounds (machinery hum, alarms, process noises) can further increase immersion and realism.
- Cutaway Features: Designing sections of the model to be removable or transparent reveals the internal workings of equipment or the layout within buildings. This is great for explaining hidden processes.
- Take-Apart Features: Building the model in modular sections allows for easier transport and enables viewers to lift off roofs or sections to see inside different levels or areas.
- Digital Interfaces: Linking the model to touchscreens or tablets allows users to trigger animations, control lighting scenarios, or access detailed information about specific components.
Interactive elements transform a model from a static display into an engaging storytelling tool, making complex processes immediately understandable and memorable.
Phase 7: Testing, Evaluation, and Iteration
Before a model is considered complete, it must undergo rigorous testing and evaluation.
- Functional Testing: Ensuring all moving parts operate smoothly, lights function correctly, and any special effects trigger as intended.
- Ergonomic Testing (for prototypes): If the model represents a product to be handled, assessing its usability, comfort, and ease of operation.
- Aesthetic Evaluation: Reviewing the model’s overall appearance, finish quality, color accuracy, and adherence to the design specifications.
- Flaw Identification: Carefully inspecting for any defects, inaccuracies, poorly fitting parts, or blemishes in the finish.
- Iteration as a Key Principle: Based on testing results and feedback, adjustments are made. This might involve minor touch-ups, remaking certain parts, or even rethinking aspects of the design. Iteration is fundamental to achieving high quality.
Phase 8: Final Presentation and Documentation
The final step involves delivering the completed model and associated materials.
- Presentation to Stakeholders: Showcasing the finished model to the client, investors, or relevant teams.
- Creating Supporting Documentation: Providing relevant drawings, technical specifications, operating instructions (for interactive models), photographs, or reports.
- Obtaining Feedback and Approval: The model serves as a final point of discussion and validation, crucial for gaining sign-off for subsequent project phases like mass production.
Key Characteristics Defining High-Quality Industrial Models
What elevates an industrial model from merely adequate to truly exceptional? It’s a combination of several defining characteristics:
Accuracy and Precision: The Foundation
- Faithful Scale Representation: Meticulous adherence to the specified scale, ensuring all proportions and dimensions accurately reflect the original object or facility.
- Scrupulous Attention to Detail: Capturing the complexity of the subject matter, including small components, textures, and intricate features, demonstrating thoroughness and understanding .
Realism and Material Authenticity
- Convincing Surface Simulation: Skillful use of paints, textures, and finishes to realistically mimic materials like aged metal, rough concrete, smooth plastic, or clear glass.
- Accurate Color and Branding: Precise matching of color schemes, logos, and signage according to the client’s specifications or real-world references.
Functionality and Interactivity (Where Applicable)
- Smooth Operation: Any moving parts or mechanisms function reliably and smoothly, without sticking or hesitation.
- Effective Use of Effects: Lighting, sound, and simulated effects are integrated purposefully to enhance understanding and impact, rather than being merely decorative .
- Intuitive Interaction: Controls for interactive features are user-friendly and clearly labeled .
Durability and Craftsmanship
- Robust Construction: Built to withstand reasonable handling, transport (especially for trade shows), and display over time .
- Quality Materials: Use of appropriate, high-quality materials that ensure longevity, prevent warping or degradation, and maintain appearance.
- Professional Finish and Assembly: Clean joints, no visible glue marks, flawless paintwork, and meticulous assembly reflect high standards of craftsmanship.
Customization and Purpose Alignment
- Tailored to Specific Needs: The model is designed and built to precisely meet the client’s unique objectives, whether for engineering review, marketing impact, or training effectiveness.
- Strategic Scale Manipulation: Deliberate scaling (up or down) to best showcase the necessary details or overall concept.
- Emphasis on Key Features: Using techniques like cutaways, highlighting, or selective detailing to draw attention to the most important aspects of the design or process.
“A model maker needs to fully understand the principles in advance and then turn the operating process into a physical object.” – This highlights the importance of purpose alignment and understanding.
The Multifaceted Benefits of Utilizing Industrial Models (Detailed Exploration)
We’ve touched upon the advantages, but let’s delve deeper into the specific, tangible benefits that industrial models bring to various aspects of a project lifecycle. These aren’t just theoretical gains; they translate into real-world improvements in efficiency, communication, and outcomes.
Benefits in Design, Planning, and Engineering
- Superior Visualization: Nothing beats a physical model for understanding complex spatial arrangements. How pipes route around equipment, how much clearance exists for maintenance access, how different building levels interact – it all becomes intuitively clear. This reduces assumptions and misinterpretations common with 2D drawings.
- Early Error Detection & Risk Mitigation: Models act as a crucial “sanity check.” Design flaws, potential equipment clashes, inefficient layouts, or safety hazards that might be missed on paper or screen often become glaringly obvious in a 3D physical form. Catching these early saves enormous time and money compared to fixing them during construction or operation.
- Workflow Optimization: By visualizing the entire process – material input, transformation stages, output, personnel movement – teams can identify bottlenecks, streamline paths, optimize workstation layouts, and ultimately increase throughput and efficiency.
- Design Testing & Iteration: Models provide a low-cost platform for experimenting with different design options. Want to see how a different machine arrangement impacts flow? Build a quick model variation. This iterative process allows for design refinement and optimization before committing significant resources.
- Enhanced Safety Planning: Visualizing the physical layout helps immensely in planning for safety. Identifying hazardous zones, planning clear evacuation routes, ensuring adequate safety clearances around machinery, and designing effective safety barriers becomes much more concrete and effective.
- Space Utilization Analysis: Models allow planners to maximize the effective use of expensive industrial space, ensuring logistics areas, production lines, storage zones, and administrative blocks are positioned optimally for performance.
- Aiding Site Selection & Terrain Integration: For new facilities, a model incorporating the site’s topography helps designers understand how the buildings interact with the landscape, plan grading, optimize views, and address potential site challenges.
Essentially, an industrial model acts as a physical simulation, allowing you to “build it small” before you “build it big,” catching errors and optimizing design in a low-risk environment.
Benefits in Communication and Collaboration
- Bridging Understanding Gaps: Technical blueprints can be opaque to non-engineers. A model provides a common, easily understood language for investors, clients, marketing teams, regulatory bodies, and the public. It makes the project accessible.
- Facilitating Clearer Communication: When architects, engineers, contractors, and owners gather around a model, discussions become more focused and productive. Everyone is looking at the same representation, reducing ambiguity and misunderstandings.
- Enhancing Collaboration: A shared physical representation encourages interaction and collaborative problem-solving. Team members can point to specific areas, suggest changes, and gain immediate feedback in a way that digital reviews sometimes lack.
- Streamlining Approvals: When decision-makers can clearly see and understand what is being proposed, approvals (whether internal budget approvals or external regulatory ones) are often granted more quickly and with greater confidence.
Benefits in Sales, Marketing, and Fundraising
- Powerful Presentation Tool: A well-crafted model makes a professional and memorable impact in boardrooms, sales pitches, and client presentations. It demonstrates commitment and allows for a compelling visual narrative.
- Trade Show Attraction: In a crowded exhibition hall, a detailed, possibly interactive model is a showstopper. It draws visitors to the booth, sparks conversations, and leaves a lasting impression long after the flyers are discarded.
- Effective Product/Process Demonstration: Explaining a complex piece of machinery or an intricate process becomes much easier with a model. Features can be pointed out, operations simulated (if interactive), and benefits clearly visualized. The Benz factory model showing car assembly is a prime example.
- Storytelling: Models transform abstract concepts or technical specifications into a tangible story that resonates with the audience, making the product or project more relatable and desirable.
- Aiding Fundraising Efforts: For startups or companies seeking investment, a compelling model can be crucial in convincing investors of the project’s feasibility, scale, and potential, making the pitch far more persuasive than drawings alone.
“An industrial model is a way to sell your product by presenting its unique features in a way that everyone can understand… The goal of the model is to draw people in, and help them understand what you are selling.”
Benefits in Training and Education
- Safe Training Environment: New employees or trainees can familiarize themselves with complex machinery, plant layouts, or safety procedures using a model without the risks associated with operating real equipment or entering potentially hazardous live environments.
- Hands-On Learning: Interacting with a physical representation aids comprehension and retention far better than studying diagrams or manuals alone. Understanding spatial relationships and process flows becomes intuitive.
- Educating Diverse Audiences: Models are excellent tools for educating not just employees, but also customers, students visiting a facility, or community groups about industrial operations or infrastructure projects.
Financial Benefits
- Cost Efficiency Through Error Prevention: The cost of building a model is typically minuscule compared to the cost of fixing design errors during or after construction/production. Early detection saves significant rework expenses.
- Optimizing Capital Investment: Ensuring the planned layout and infrastructure truly support maximum productivity and efficiency represents a better return on the substantial investment required for industrial facilities.
- Reducing Exhibition Costs: Transporting and setting up a scaled model of large, heavy equipment at a trade show is vastly cheaper and logistically simpler than bringing the actual machine.
Diverse Applications: Where Industrial Models Make a Difference
The versatility of industrial models means they find applications across a vast spectrum of industries. Wherever complex physical systems, processes, or structures need to be visualized, planned, or communicated, a model can provide significant value.
Manufacturing Sector Applications
- Factory and Plant Layout Planning: The classic application – optimizing the arrangement of machinery, assembly lines, storage, and support areas for efficient flow and space utilization.
- Production Line Simulation and Optimization: Visualizing material flow, buffer zones, workstation interactions, and potential bottlenecks on assembly or processing lines.
- Equipment Design Prototyping and Demonstration: Creating scale models or full-size mock-ups of new machines, tools, or robotic cells for design review, ergonomic testing, and sales demonstrations.
- Specific Examples: Automotive plants, Pharmaceutical/Biologics facilities, Electronics assembly, Food processing units.
Energy Sector Applications
- Power Plant Design: Visualizing layouts for nuclear facilities, fossil fuel plants, steam generation plants, and associated infrastructure like cooling towers and switchyards.
- Renewable Energy Installations: Planning the layout of large solar farms (photovoltaic parks) or wind turbine arrays, including access roads and substations.
- Oil and Gas Industry: Modeling complex offshore platforms (oil rigs), onshore refineries, pipelines, and storage tank farms.
- Bio-recycling / Bio-fuel Plants: Representing the processes and equipment involved in converting waste or biomass into energy or recycled materials.
Logistics and Transportation Applications
- Warehouse and Distribution Center Layouts: Planning racking systems, conveyor belts, sorting areas, loading docks, and traffic flow within large logistics facilities.
- Logistics Hubs: Modeling intermodal transfer points, cargo handling facilities, and administrative buildings.
- Seaport and Airport Infrastructure Projects: Visualizing terminal layouts, container yards, piers, runways, baggage handling systems, and associated road/rail connections.
- Transportation Infrastructure: Modeling complex freeway interchanges, railway yards, bridges, and tunnel systems.
Construction and Civil Engineering Applications
- Building Design Visualization: Creating architectural models that show not just the exterior but also internal layouts, structural systems, or MEP (Mechanical, Electrical, Plumbing) routing.
- Major Infrastructure Projects: Models of dams, bridges, water filtration systems, and other large-scale civil works.
- Site Planning and Development: Showing how proposed buildings or developments fit within the existing terrain and surrounding context.
Process Industries Applications
- Water Treatment / Sewage Plants: Illustrating the different stages of treatment, including settling tanks, aeration basins, filter beds, and pumping stations.
- Chemical Processing Facilities: Visualizing complex arrangements of reactors, distillation columns, storage tanks, and intricate piping networks.
- Distilleries / Breweries: Showcasing unique architectural designs combined with the process equipment involved in production.
Other Diverse Applications
- Aerospace and Defense: Models of satellites, aircraft components, military vehicles, or training simulators.
- Showcasing Specific Machinery: Creating detailed models (often cutaways) of engines, pumps, valves, turbines, or transmissions for sales, training, or exhibition purposes.
- Architectural Planning Scale Rendering: Using massing models early in the architectural design process to study form, scale, and context.
- Museum Exhibits and Educational Displays: Using models to explain historical industrial processes or complex technologies to the public.
The Role of Technology in Revolutionizing Industrial Model Making
While traditional craftsmanship remains vital, modern technology has dramatically transformed the capabilities, speed, and precision of industrial model making. The synergy between skilled hands and advanced tools enables the creation of models that were previously unimaginable.
Computer-Aided Design (CAD) Software
- The Digital Foundation: CAD is the starting point for virtually all modern, high-precision models. It allows for exact digital construction, ensuring accuracy from the outset.
- Enabling Complexity: Software easily handles complex curves, intricate assemblies, and organic shapes that would be difficult or impossible to draft by hand.
- Seamless Integration: CAD files directly drive manufacturing processes like 3D printing and CNC machining, ensuring a smooth transition from digital design to physical part.
Additive Manufacturing (3D Printing)
Perhaps the most transformative technology in recent years, 3D printing offers unparalleled advantages:
- Enhanced Accuracy, Speed, and Efficiency: Especially for complex, one-off, or small-batch parts, 3D printing can produce components much faster and often more accurately than traditional methods. It’s the cornerstone of “Rapid Prototyping.”
- Feasibility of Intricate Geometries: Undercuts, internal channels, fine lattices, and highly detailed surfaces can be created directly, layer by layer. The Macallan Distillery model reportedly had 380,000 individual components, likely heavily reliant on 3D printing.
- Diverse Material Options: A wide range of plastics (Nylon, ABS, PLA), high-resolution resins (UV-cured photopolymers), flexible materials, composites, and even full-color binder jetting are available.
- Supplementing Traditional Methods: 3D printing often works alongside conventional techniques, providing highly detailed elements that are then integrated into a larger, traditionally built model.
Subtractive Manufacturing (CNC Machining, Laser Cutting)
- High Accuracy for Robust Parts: CNC (Computer Numerical Control) milling and turning excel at creating precise, strong parts from solid blocks of metal, plastic, or wood.
- Working with Diverse Materials: These methods handle materials that might be difficult or impossible to 3D print effectively, particularly metals requiring high strength.
- Laser Cutting Precision: Ideal for quickly and accurately cutting flat sheet materials (acrylic, thin wood, card) for facades, structural layers, templates, or intricate patterns.
Advanced Visualization Technologies
Beyond creating the physical object, technology enhances how we interact with and understand models:
Technology | Description | Benefit in Model Making Context |
---|---|---|
Virtual Prototyping (VP) | Creating and testing purely digital simulations of models or systems without physical construction. | Saves significant time and cost in early design stages; allows complex analyses (stress, flow) impossible on a physical model. |
Augmented Reality (AR) | Overlaying digital information (text, animations, data) onto the view of the real physical model using a smartphone, tablet, or AR glasses. | Can show hidden details, simulate processes dynamically, display operational data, or visualize design variants without altering the physical model. Enhances understanding. |
Virtual Reality (VR) | Immersive experience within a fully digital 3D environment representing the model or facility, viewed through VR headsets. | Allows virtual walkthroughs at 1:1 scale, ergonomic assessments, immersive training scenarios, and collaborative design reviews in a shared virtual space. |
Real-time Digital Twins | A dynamic digital replica connected to its physical counterpart, reflecting real-time data and status (or vice-versa). | Potential to link physical models with live sensor data or simulations for enhanced monitoring and interaction, though still emerging for physical display models. |
Integration and Workflow Synergy
The true power lies in the intelligent combination of these technologies. A typical modern workflow might involve: CAD design -> 3D printing intricate details -> CNC machining structural parts -> Laser cutting flat panels -> Hand assembly and finishing -> Potentially adding AR markers for enhanced digital interaction. Choosing the right tool for each specific part of the model optimizes quality, speed, and cost.
Common Challenges in Industrial Model Making and How to Overcome Them
Despite the advancements, creating exceptional industrial models still presents challenges. Awareness and proactive strategies are key to navigating them successfully.
Blueprint Interpretation Errors
- The Challenge: Misreading or misinterpreting complex technical drawings leads to inaccuracies in the model.
- Overcoming It: Requires meticulous cross-checking of drawings, asking clarifying questions early, and fostering close communication between the design team and the model makers. Double-checking critical dimensions is crucial.
Material Inconsistencies and Selection Issues
- The Challenge: Materials may behave unexpectedly (warping, shrinking, poor paint adhesion, brittleness), or the wrong material is chosen for the application.
- Overcoming It: Deep knowledge of material properties is essential. Performing test prints or small material samples can verify suitability. Selecting materials based on required strength, detail level, finish, and environmental conditions (e.g., transport, display lighting).
Achieving Scale Accuracy with Complex Details
- The Challenge: Replicating extremely fine details accurately at a reduced scale can be difficult. Some features might become too small or fragile.
- Overcoming It: Utilizing high-resolution technologies like SLA/DLP 3D printing. Sometimes, slight, approved simplifications of non-critical details are necessary. Exceptional hand-finishing skills are vital for refining tiny components.
Integrating Functional and Interactive Elements Reliably
- The Challenge: Ensuring motors run smoothly, lights work consistently, and complex mechanisms don’t fail, especially after transport. Wiring and power supply need careful planning.
- Overcoming It: Careful design of mechanical linkages and electronic circuits. Using high-quality, reliable components (motors, LEDs, controllers). Thorough testing of all interactive features before final assembly and shipping. Providing clear operating instructions.
Time and Budget Constraints
- The Challenge: Clients often have tight deadlines and fixed budgets, which can put pressure on the quality and scope of the model.
- Overcoming It: Requires realistic project planning and quoting from the start. Clearly defining the scope of work and level of detail. Utilizing efficient techniques like rapid prototyping where appropriate. Maintaining open communication with the client regarding progress and potential issues impacting timeline or budget.
Anticipating these challenges and having strategies to address them distinguishes experienced, professional model makers.
The Future of Industrial Model Making: Trends and Innovations
The field of industrial model making is constantly evolving, driven by technological advancements and changing industry needs. Here are some key trends shaping its future:
Increasing Integration of Digital and Physical (“Phygital” Experiences)
- Augmented Reality (AR) overlays will become more common, allowing viewers to point a device at a physical model and see dynamic data, animations, or internal views superimposed.
- The concept of Digital Twins – linking a physical model to real-time data streams from the actual facility or simulation software – offers exciting possibilities for interactive displays and monitoring.
Advancements in Materials Science
- Development of new 3D printing materials with improved strength, flexibility, conductivity, temperature resistance, or even more realistic textures and finishes.
- Greater availability and use of sustainable and biodegradable materials for model construction.
AI-Based Simulation and Design Assistance
- Artificial intelligence could potentially assist in optimizing designs digitally *before* model making begins, identifying potential issues or suggesting improvements based on simulation data.
- AI might also help automate certain aspects of the digital modeling process itself.
Greater Accessibility of Advanced Technologies
- The decreasing cost of high-quality 3D printers, laser cutters, and powerful CAD software makes sophisticated model making accessible to a wider range of companies and even smaller studios.
Emphasis on Sustainability in Model Making
- Growing awareness will likely drive increased demand for models built using environmentally friendly materials (like plant-based plastics) and energy-efficient fabrication processes. Waste reduction during production will also be a focus.
Choosing the Right Industrial Model Maker: What to Look For
Selecting the right partner to create your industrial model is crucial for achieving a result that meets your expectations and objectives. Here’s a checklist of factors to consider:
Selection Criterion | Key Considerations / Questions to Ask |
---|---|
Expertise and Relevant Experience | Does the company specialize in your industry (e.g., energy, manufacturing, architectural)? Can they demonstrate successful projects similar to yours? How long have they been in business? |
Portfolio Review | Carefully examine examples of their past work. Does the quality, detail, and style align with your needs? Pay attention to finish, accuracy, and complexity. |
Understanding of Principles | Does the team seem to grasp the underlying engineering, architectural, or process principles they need to represent? Can they “speak your language”? |
Technological Capabilities | What fabrication technologies do they utilize (3D printing types, CNC, laser)? Do they have the right equipment for the level of detail and materials your project requires? |
Craftsmanship and Attention to Detail | Is there evidence of meticulous hand-finishing, clean assembly, and overall high-quality craftsmanship in their portfolio? |
Communication and Collaboration Process | How do they communicate during the project? Are they responsive? Do they involve you in key decisions and provide progress updates? Is there a clear point of contact? |
Ability to Customize and Problem-Solve | Are they flexible and able to tailor solutions to your specific, potentially unique requirements? Can they offer creative solutions to challenges? |
Quality of Materials and Durability Focus | Do they use high-grade, durable materials suitable for the intended use (e.g., transport, frequent handling)? Do they discuss material choices clearly? |
Note: Look for model makers who ask insightful questions about your project goals. Reputable companies often showcase their work online (like the examples potentially attributed to Shree Creators, KiwiMill, RJ Models, Architype3D® in the source). Don’t hesitate to ask for references.
Pro Tip: Obtain detailed quotes from multiple potential suppliers. Compare not just the final price, but also the proposed approach, materials, level of detail offered, estimated timeline, and your overall confidence in their ability to deliver.
Conclusion: The Enduring Value of Physical Representation in an Increasingly Digital World
In conclusion, industrial models are far more than just scaled-down objects. They are dynamic, multifaceted tools essential for navigating the complexities of modern industry. They serve as crucial aids in visualization, indispensable bridges for communication, rigorous platforms for testing, and powerful instruments for persuasion.
In an era dominated by digital screens and virtual simulations, the tangible, physical presence of a well-crafted model retains a unique and enduring power. It fosters intuitive understanding, facilitates collaborative problem-solving, and leaves a lasting impression in a way purely digital representations often cannot. By harnessing the synergy between time-honored craftsmanship and cutting-edge technology, industrial models help organizations minimize risk, optimize designs, save costs, and ultimately achieve greater success. Whether clarifying a complex process, securing vital funding, or inspiring the next generation of engineers, the industrial model remains a vital and valuable asset, proving that sometimes, seeing (and touching) truly is believing.
Frequently Asked Questions (FAQs) About Industrial Models
Here are answers to some common questions people have about industrial models:
- What materials are best for industrial models?
- There’s no single “best” material. The choice depends heavily on the model’s purpose, required detail, durability needs, budget, and fabrication method. Common options include various plastics (acrylic, PVC, ABS), foam, wood, metals, and specialized 3D printing resins. A good model maker will recommend the most suitable materials for your specific project.
- How long does it take to create an industrial model?
- Production time varies significantly based on size, complexity, level of detail, interactivity, and the chosen fabrication techniques. It can range from a few days for a simple conceptual model to several weeks or even months for large, highly detailed, interactive exhibits.
- What does an industrial model cost?
- Costs are highly variable. Factors include size, complexity, materials, required precision, interactive features, and the labor involved. Prices can range from a few hundred dollars for very simple models to tens or even hundreds of thousands of dollars for extremely large, intricate, and technologically advanced creations. Always get a custom quote.
- How does 3D printing compare to traditional model-making methods?
- 3D printing excels at creating complex geometries quickly and accurately, especially for smaller parts or prototypes. Traditional methods like CNC machining are better for high-strength metal parts, while handcrafting offers unique customization and finishing. Often, the best results come from combining these techniques, leveraging the strengths of each.
- Can industrial models be interactive?
- Yes, definitely! Many modern models incorporate features like LED lighting, moving parts (conveyors, turbines), sound effects, or even simulated smoke or water flow to dynamically demonstrate processes and increase engagement.
- How are models used specifically in factory planning?
- They are crucial for visualizing equipment layouts, analyzing material and personnel flow, identifying potential bottlenecks or safety hazards, testing different configurations, and communicating the proposed plan clearly to all stakeholders before committing to construction.
- Do I need formal training to make industrial models?
- While formal training (like a technical model maker apprenticeship or degrees in design/engineering) is beneficial, it’s not strictly required. Many skilled model makers have developed their expertise through experience, practice, a good eye for detail, excellent hand skills, and a strong understanding of technical drawings and fabrication processes.
- What scale should my industrial model be?
- The optimal scale depends on the model’s purpose, the size of the original object, the level of detail needed, and where it will be displayed. Common scales range widely, for example: 1:10 or 1:20 for small equipment, 1:50, 1:100, or 1:200 for buildings or factory sections, and 1:500, 1:1000, or even smaller for large sites or infrastructure projects.
Let’s Bring Your Vision to Life
Ready to explore how a custom industrial model can benefit your project? Whether you need enhanced visualization for planning, a compelling tool for sales, or an effective aid for training, our expert team is here to help. We combine cutting-edge technology with meticulous craftsmanship to create models that communicate clearly and make a lasting impact.
Contact us today to discuss your specific requirements and discover how we can transform your blueprints and ideas into a tangible, powerful representation.
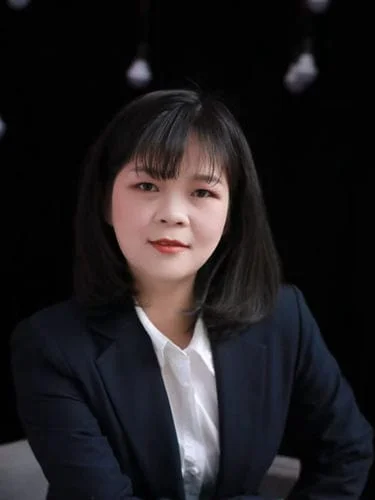